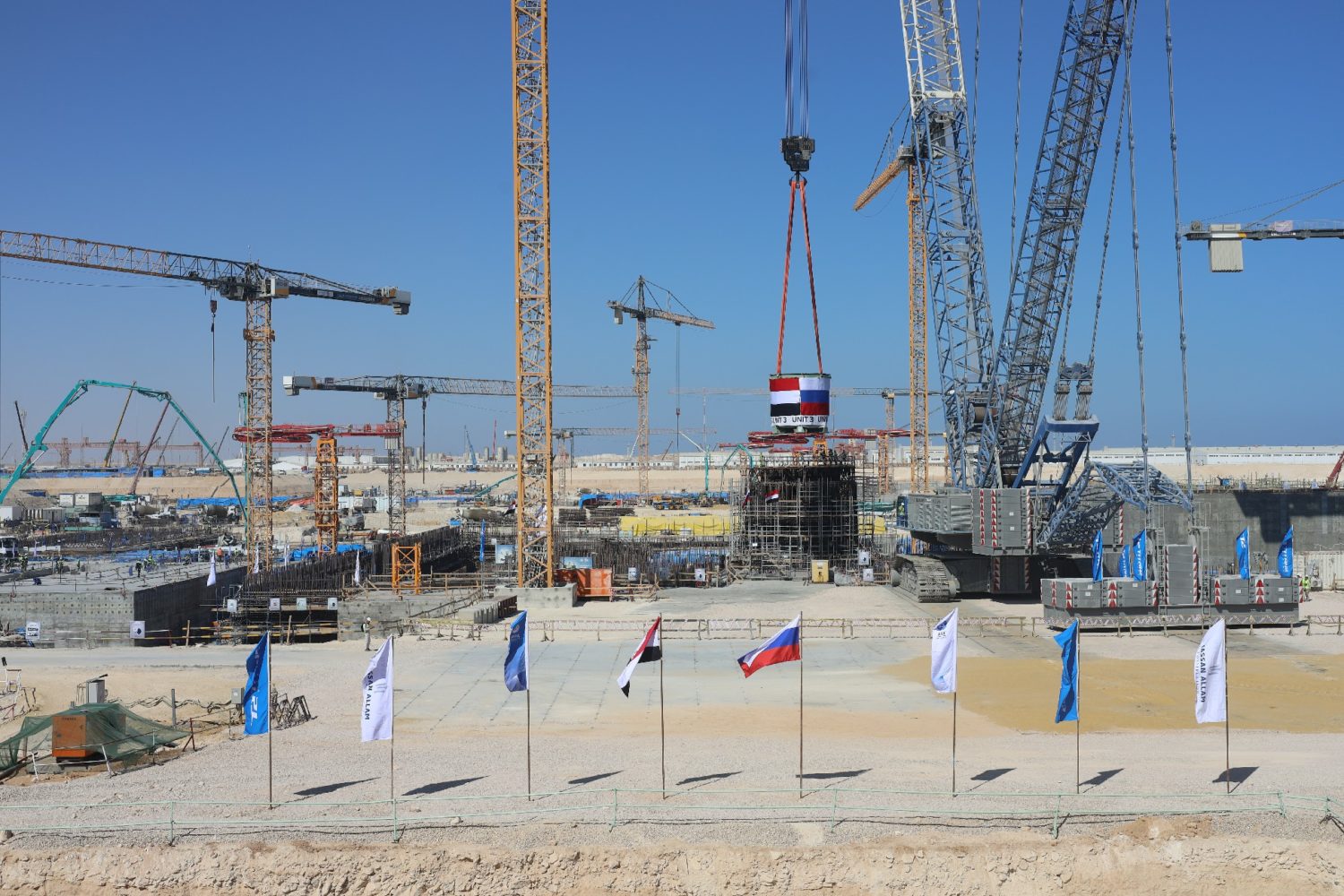
Главный приоритет — безопасность
вернуться к содержаниюВ начале октября на третьем блоке строящейся в Египте АЭС «Эль-Дабаа» начался монтаж корпуса устройства локализации расплава (УЛР, или так называемой ловушки расплава). Это одно из ключевых событий на стройплощадке в этом году.
В торжественной церемонии принял участие председатель Совета директоров Управления по атомным электростанциям Египта Амгед Эль-Вакиль.
«В приоритете для Египта — ядерная и физическая безопасность. Устройство локализации расплава — один из основных элементов систем безопасности на АЭС «Эль-Дабаа», и это отражает высочайший уровень ядерной безопасности для обеспечения безопасной и непрерывной работы станции», — отметил Амгед Эль-Вакиль.
Монтаж ловушки проходил с помощью тяжеловесного крана грузоподъемностью 2 тыс. т. Вице-президент АО «АСЭ», директор проекта по сооружению АЭС «Эль-Дабаа» Алексей Кононенко подчеркнул, что работы по монтажу начались в соответствии с графиком. «Все это было бы невозможным без всестороннего сотрудничества египетского заказчика и генподрядчика. Хочу выразить глубокую благодарность каждому, кто приложил усилия к достижению этого производственного этапа на нашем проекте», — отметил Алексей Кононенко.
Ловушка расплава — это оборудование длительного цикла изготовления. Она состоит из нескольких элементов, общий вес которых 480 т (при этом вес корпуса устройства локализации расплава — 155 т). Груз с компонентами УЛР был доставлен в морской порт площадки строительства АЭС «Эль-Дабаа» в середине лета.
А в конце сентября на площадке второго блока начался еще один важный строительный этап: строители приступили к возведению внутренней защитной оболочки (ВЗО) реакторного здания. Монтаж блока ВЗО — сложный технологический процесс. Он длится около 15 часов и выполняется в несколько этапов тяжеловесным краном грузоподъемностью 1350 т.
«Устройство гермооболочки здания реактора — это трудоемкий процесс, результатом которого будет безопасная эксплуатация будущей АЭС», — отметил Алексей Кононенко.
Внутренняя защитная оболочка состоит из шести ярусов, в первом ярусе — 12 укрупненных блоков (составных конструктивных элементов). Вес каждого из блоков — от 60 до 80 т. Эти блоки изготавливаются на производственной базе АЭС «Эль-Дабаа» специалистами подрядной организации.
Из России в Египет
Российские атомщики продолжают изготавливать для египетской атомной станции все необходимое оборудование.
В конце сентября специалисты волгодонского «Атоммаша» (машиностроительный дивизион Росатома) начали производство корпуса реактора для второго блока «Эль-Дабаа». Заготовки для корпуса были отлиты на металлургическом заводе машиностроительного дивизиона в Санкт-Петербурге и доставлены на производственный комплекс в Волгодонске. Там детали корпуса соберут воедино. Параллельно на заводе продолжается изготовление реакторного оборудования для первого блока АЭС «Эль-Дабаа».
На машиностроительном заводе в Карелии — «Петрозаводскмаше» — идет изготовление корпусов главных циркуляционных насосных агрегатов (ГЦНА), которые обеспечивают циркуляцию теплоносителя в первом контуре реактора. Кроме корпусов насосов для АЭС «Эль Дабаа», на площадке будут изготовлены плакированные трубы, узлы главного циркуляционного трубопровода (ГЦТ) и компенсатор давления.
В общей сложности производственные площадки машиностроительного дивизиона изготовят и поставят для «Эль-Дабаа» порядка 12,5 тыс. т оборудования. Это атомные реакторы с внутрикорпусными устройствами и верхним блоком, комплекты парогенераторов, корпуса ГЦНА, ГЦТ, оборудование для активной и пассивной систем защиты атомных реакторов и компенсаторы давления.
28 сентября в России отметили День работника атомной промышленности. В преддверии профессионального праздника атомщиков сталевары «АЭМ-Спецсталь» (машиностроительный дивизион Росатома) произвели разливку «первой» стали для корпуса реактора четвертого блока АЭС «Эль-Дабаа». Металлурги выплавили 192 т металла, из которых в дальнейшем будет изготовлена часть корпуса реактора ВВЭР-1200. Операция проходила в сверхмощной сталеплавильной печи, где за 2-3 часа работы можно выплавить 120 т металла. После разливки металл был направлен на внепечную обработку, а после — на двое суток в вакуумную камеру, чтобы остыть до 550–650 °C.