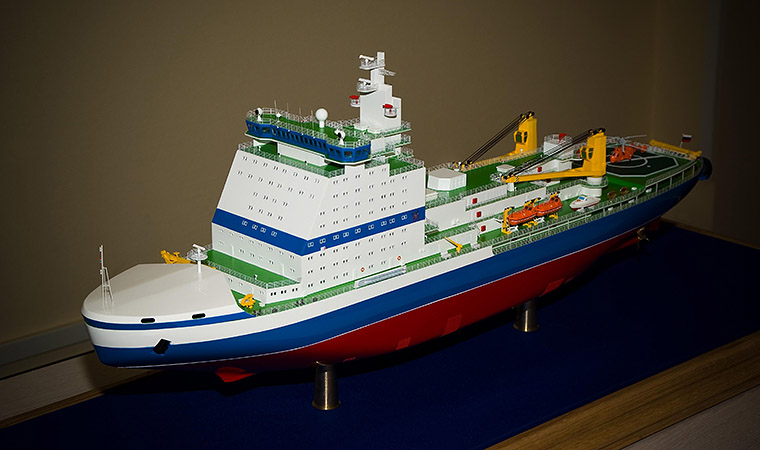
Unique welding job
back to contentsA Project 22220 flagship icebreaker is being built at the Baltic Plant in Saint Petersburg, with construction of two other ships to begin soon. The new generation nuclear icebreaker features increased capacity. With 60MW even at full load, it outperforms the existing Arktika type icebreakers having only 54 MW. Besides, the flagship is wider, which means a wider track in the ice for the caravan. New hull lines allow traveling through 2.9m thick ice while Arktika can make its way through 2.25m ice only. In other words, the icebreaker will be able to go the entire Northern Sea Route almost all year round. The new generation vessel will feature passive safety systems and have a 55-strong crew, which is almost two times less than Arktika has.
With a new RITM-200 reactor, the refueling interval will increase from the current 4–6 years up to 8–10 years to significantly decrease fuel costs. Subsidiaries of Atomenergomash, Rosatom’s nuclear engineering division, cover the entire process of RITM-200 development – from the reactor design to manufacturing and installation. The design was developed by the Afrikantov Experimental Design Bureau for Mechanical Engineering (OKBM Afrikantov) while ZiO-Podolsk is responsible for manufacturing. Recently, the latter did a unique job of welding steam manifolds to the reactor vessel.
To weld them together, a very complicated method was used by placing them in a fixed position and heating up the assembly area. This method is applied in specific situations, when components cannot be handled and the seam is hard to reach.
The welding process went on for three days without breaks. To avoid cracks, the material was heated up to 200°С. After the welding was completed, the joined components were heat-treated at 650°С for more than 24 hours and then machined. Following the welding quality testing with non-destructive X-ray methods in the plant laboratory, weld seams were found to comply with the strictest standards.
Engineers are now preparing for the final assembling operations on the reactor. “The visit to the production plant left a positive impression on me. Manufacturing practices improve, and so does the equipment used in the production process. With a production planning system in place, I am sure that ZiO-Podolsk will ship all the components for the flagship icebreaker in accordance with the schedule,” said Sergei Chernogubovsky, Project 22220 Manager at the Baltic Plant.
“ZiO-Podolsk has done a great job to produce the RITM-2000 reactor vessel components. It is clear that the task will be completed in time,” Dmitri Zverev, OKBM Afrikantov CEO and Chief Designer, noted at a working meeting.
Atomenergomash CEO Andrei Nikipelov stressed the fact that the work went on “with a strict compliance with the time schedule and the contract.”