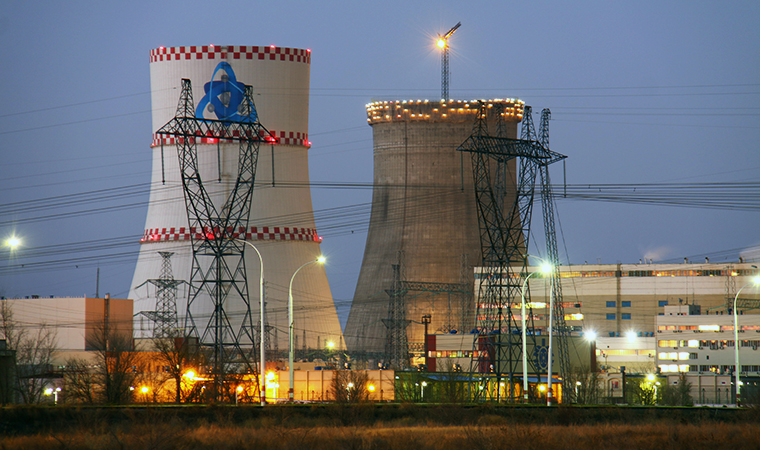
Construction of scale
back to contentsNovovoronezh NPP Unit 6 prepares for a trial run with over 100 stress tests to be done within just 50 days before the reactor is put into operation. Ten thousand people work on the construction site in these days. “We have brought together an enormous team – technicians, erection and installation staff, maintenance workers and many others. There is enough work for everyone. Many leave the site at midnight and are back already at 7 am,” says Mikhail Pinchuk, Deputy Director for Heating Installations at the local office of Atomenergoproekt (NPP General Contractor).
Preparations for the commissioning began in the summer when dummy fuel assemblies were loaded into the reactor. They are exact copies of operational fuel assemblies but, instead of nuclear fuel, contain another substance imitating the real fuel performance. “The number of dummies is the same as the number of fuel assemblies – there are 163 of them,” Mikhail Pinchuk explains. Dummy assemblies are used to imitate dimensions, weights and hydraulic properties of real fuel assemblies during the commissioning phase. Dummies will be replaced as soon as engineers are sure that all the equipment works as it should, right before the reactor startup scheduled for the year end.
The hot testing phase will begin after the reactor is started, to check the reliability of circulation pumps at load, auxiliary power supply and reactor safety systems. “Hot tests simulate normal operation of the unit except that turbines do not rotate and no power is generated,” Mikhail Pinchuk continues.
“If compared to Rostov, the commissioning of Novovoronezh NPP is a third more complicated. We are building here a new station, not a single unit, which requires different solutions to adopt,” says Mikhail who has taken part in the commissioning of three units at Rostov NPP and the fourth unit at the Kalinin NPP. According to him, hot tests of VVER-1200-based units do not differ much from tests of VVER-1000 reactors (AES-92 design used at the Kalinin NPP and Rostov NPP). The test scope and procedures are the same, except for the number of safety systems. For example, the improved design provides for a new core catcher that will keep molten nuclear fuel inside the core in case of a beyond design basis accident.
160 Tons Of Safety
The remaining large-size equipment was finally delivered to the Leningrad NPP-2 construction site in early September. Petrozavodskmash shipped a mammoth 160-ton vehicle air lock, 10m long and 9m high. “Equipment grows as nuclear stations increase their capacity,” Mikhail Karrask, an advisor to LNPP-2 Director, noted. “The only route to transport such bulky cargo is by river and sea. It was the Volga–Baltic Waterway which enabled us to deliver all the oversized and heavyweight components for Unit One.”
The vehicle airlock is designed to cut off the reactor zone, where there is radiation, from the clean zone. It has two thick doors, 22 tons each, opening by turns. The airlock is used to take in and out nuclear fuel and reactor components when they are to be replaced.
Manufactured specially for the Leningrad NPP-2, it is a new product for Petrozavodskmash. Although the plant has never produced airlocks before, they managed to improve it. “The improved design incorporates our latest solutions enhancing the reliability and convenience of airlock operation and maintenance,” explains Pavel Danilyuk, Sales Director at Petrozavodskmash. “It has a high safety factor and is capable of sustaining an earthquake or an aircraft crash.”
Meanwhile, concrete placement for the containment, a reactor’s essential safety structure, has begun at Unit 2 of the Leningrad NPP-2. The insulation space of the containment’s double-wall thick steel cylinder will be filled with serpentine concrete, which retains moisture, has high radiation resistance, and effectively decreases the neutron flux outside of the reactor pit.
As soon as the placement is finished, concrete will be heat-treated and dried. Final quality will be checked with the neutron depth profiling technique. Concreting, drying, heat treatment and quality control procedures are planned to be completed by the end of September.
The containment will be finally installed in its permanent position in the reactor pit to surround the reactor core, where radiation reaches its maximum level. The containment will serve as a heat and radiation shield for the reactor pit’s regular concrete.
Tests passed by Rostov-3
Acceptance tests at 100% load were carried out at Rostov NPP Unit 3 in late August. All of them were passed successfully to confirm that the unit is ready for commercial operation.
A commission of the national regulator Rostekhnadzor is now working on site to issue an opinion on the compliance of Unit 3 with the project design and regulatory requirements. The work is also ongoing to draft documents to be presented to the acceptance commission of Rosenergoatom, an operator of Russian nuclear stations.
Reactor Unit 3 was started up in November 2014 and connected to the national grid in December 2014.
In the meantime, Unit 4 of the Rostov NPP is getting ready to mount the reactor vessel. All the required components are already on the site, with the support ring installed in the reactor pit. The 8-ton support ring bears the entire load of the reactor vessel and therefore needs specific attention and accuracy during the installation.
Ahead of plans
Construction of the Kursk NPP-2 began not long ago, but has gained good momentum in August as construction and installation were 5% ahead of the schedule. A strategic structure – an automobile bridge over the Seym River – was completed 9 months earlier than planned (the construction took 18 months instead of 27). The bridge will be used to deliver components and materials to the site already in November.
The work is ongoing to build a facility which will manufacture reinforced metal blocks, a construction material, and other auxiliary facilities for the construction process. In the 4th quarter of 2015, the general contractor (NIAEP) plans to begin the installation of a concrete plant to produce ready-mix concrete for the power station. Major construction works will begin as soon as a water intake facility is completed.