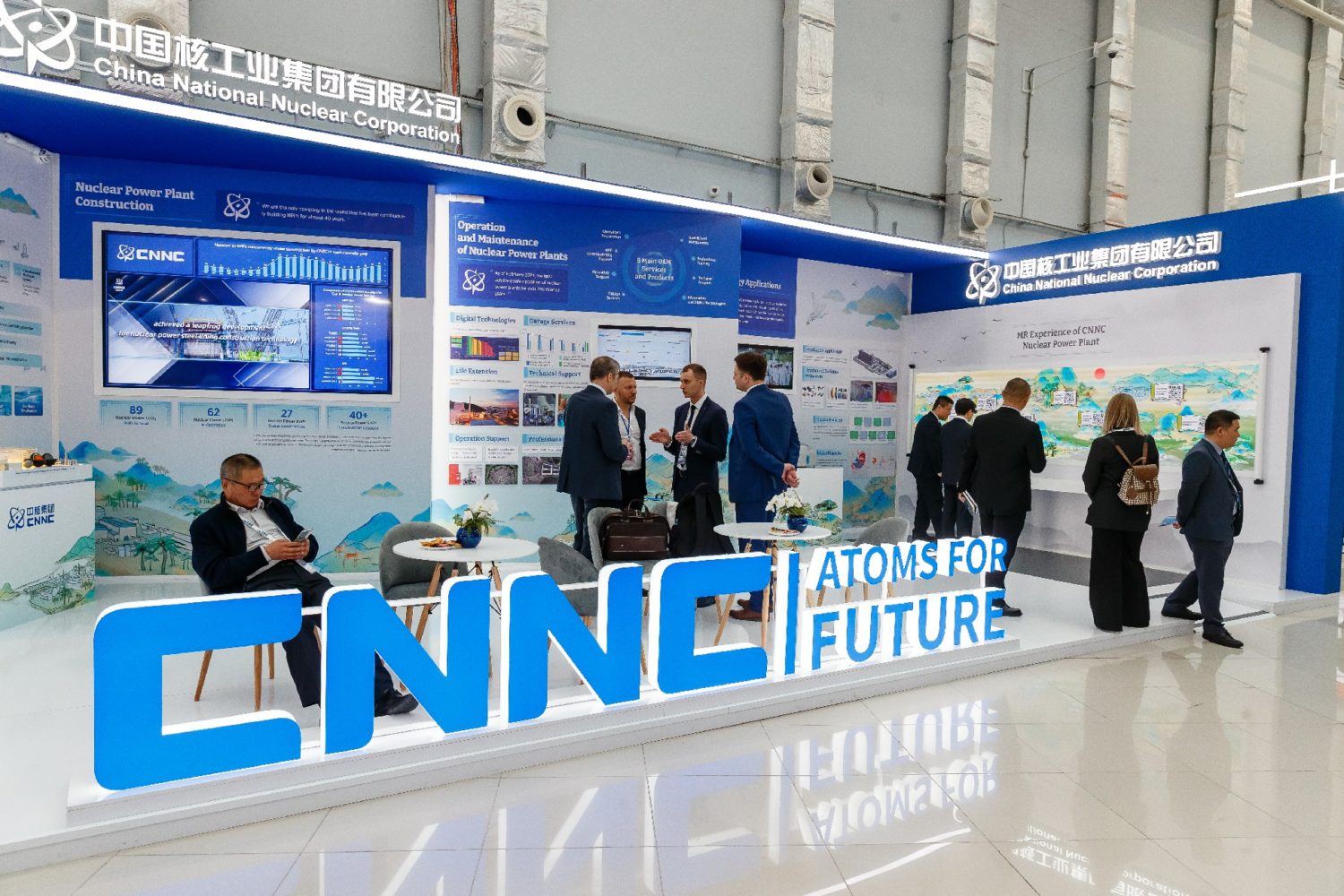
Generation IV
back to contentsThe Chinese delegation took active part in the Atomexpo 2024 international forum held in late March. For more information on the forum read other articles in this issue. Discussions at Atomexpo 2024 were centered around Generation IV technologies experiencing growth both in China and Russia.
The key idea voiced at the thematic session of the forum was that the Generation IV term extends beyond reactor technology to comprise integrated systems. Waste management and finite reserves of natural uranium were named as the two main challenges faced today by the nuclear power industry. Therefore, Generation IV systems must both meet the requirements for previous reactor generations (primarily in terms of safety) and address these two challenges.
The Generation IV International Forum (GIF IV) that brings together 14 countries, including China and Russia, and the IAEA International Project on Innovative Nuclear Reactors and Fuel Cycles (INPRO) focus on six Generation IV technologies:
1. Supercritical water-cooled reactor
2. Sodium-cooled fast reactor
3. Lead-cooled fast reactor
4. Molten salt reactor
5. Gas-cooled fast reactor
6. High-temperature gas-cooled reactor
Lead and sodium
China and Russia have a long track record of successful cooperation, including in fast neutron technology. Since 2011, China has been operating an experimental sodium-cooled fast reactor (CEFR) developed in partnership with Rosatom Group companies. Its design was used by Chinese engineers as a basis for China’s proprietary 600 MW demonstration sodium-cooled fast reactor (CFR 600). Two power units with these reactors are under construction in Fujian Province. In 2022, Rosatom supplied fuel for the initial load of Unit 1, which might achieve its first criticality as early as this year. Speaking at Atomexpo 2024, Yang Hongyi, Director General of the China Institute of Atomic Energy (CIAE), presented a CFR 1200 commercial fast reactor project. According to the speaker, the reactor will have a capacity of 1,200 MW, will be powered by MOX fuel, and is scheduled for commissioning in 2030.
As for Russia, it has achieved the most progress in the development of sodium-cooled and lead-cooled fast neutron reactors.
Its BN 600 and BN 800 sodium-cooled fast reactors operated at the Beloyarsk NPP are the world’s only commercial fast neutron reactors. BN 600 has been in operation for almost 45 years. Engineers are now considering the possibility of extending its lifetime to 60 years. The key solution in BN 600 — an integral layout of the reactor core — has become common for all subsequent fast reactor designs.
New technology solutions, particularly passive safety systems, were used in the BN 800 design. BN 600 and BN 800 do not only serve a fast technology demonstration purpose — they are also indispensable for testing new solutions for advanced fast neutron reactors. “Last year, we made a huge step forward towards closing the nuclear fuel cycle as BN 800 was fully loaded with MOX fuel. Our next step will be transition to a new type of fuel to burn minor actinides,” RosEnergoAtom CEO Alexander Shutikov announced at Atomexpo 2024.
He said that work was underway to develop an innovative power unit with a next-generation BN 1200M sodium-cooled fast reactor that will rely on the time-proven solutions from the BN 600 and BN 800 designs and new technology. BN 1200M differs from previous sodium-cooled fast reactor designs by improved safety, a longer refueling interval, higher fuel burnup, and reduced construction costs.
Another fast neutron reactor, but lead-cooled, BREST-OD 300 will be the heart of a pilot power production facility (abbreviated ODEK in Russian), now under construction as part of the Proryv (Breakthrough) Project, which will demonstrate all the advantages of Generation IV nuclear technology. ODEK will also include a uranium-plutonium fuel fabrication unit and a spent fuel reprocessing unit. New fresh fuel will be produced there from reactor-grade plutonium and depleted uranium by carbothermal synthesis. This will mark the actual closing of the nuclear fuel cycle on the nuclear plant site. ODEK is planned to be commissioned in its entirety in 2030.
Atomexpo 2024 guests had an opportunity to watch a live test run of the carbothermal synthesis line at the BREST-OD 300 fuel fabrication unit.
“Along with test-running advanced technologies for Generation IV reactors, the Proryv Project produces a horde of ground-breaking solutions for fuel fabrication and processing, which is the most complex and science-intensive chemical engineering industry,” Rosatom Director General Alexey Likhachev commented on the event. Intensive work is underway to develop a large lead-cooled reactor BR 1200 that will be powered by mixed nitride (MNUP) fuel.
Molten salt, high temp, gas cooling, and supercriticality
China is a global leader in high-temperature gas-cooled reactors. Its HTR 10 research reactor was launched in the 2000s. In late 2023, two 250 MW high-temperature gas-cooled pebble-bed modular (HTR-PM) reactors, the first in the world, were put into commercial operation at the Shidao Bay Nuclear Power Plant. They use gaseous helium as coolant.
Russia is also developing a similar technology. Rosatom is working on a large-scale project titled ‘Development of Nuclear Technology for Commercial Production and Consumption of Hydrogen’. The plan is to develop and build a pilot nuclear power plant with a high-temperature gas-cooled reactor (HTGR) and a hydrogen production facility. The technical design for the HTGR has been finalized.
Another technology — supercritical water-cooled reactors — implies the use of coolant at supercritical temperature and pressure. This will significantly improve the plant’s efficiency and economics. Rosatom is developing VVER SCR, a supercritical water-cooled power reactor. At present, tests are being conducted on structural materials for the reactor in development.
Russian engineers are also working on the design of a molten salt research reactor. This is a reactor in which nuclear fuel is dissolved in a metal fluoride salt medium (coolant), with the salt-and-fuel mixture forming a homogeneous reactor core. Unlike heterogeneous reactors, they need no fuel rods or fuel assemblies. Their primary purpose is transmutation of minor actinides. Molten salt reactors are considered to be part of the closed nuclear fuel cycle. The concept design of the reactor has been finalized.