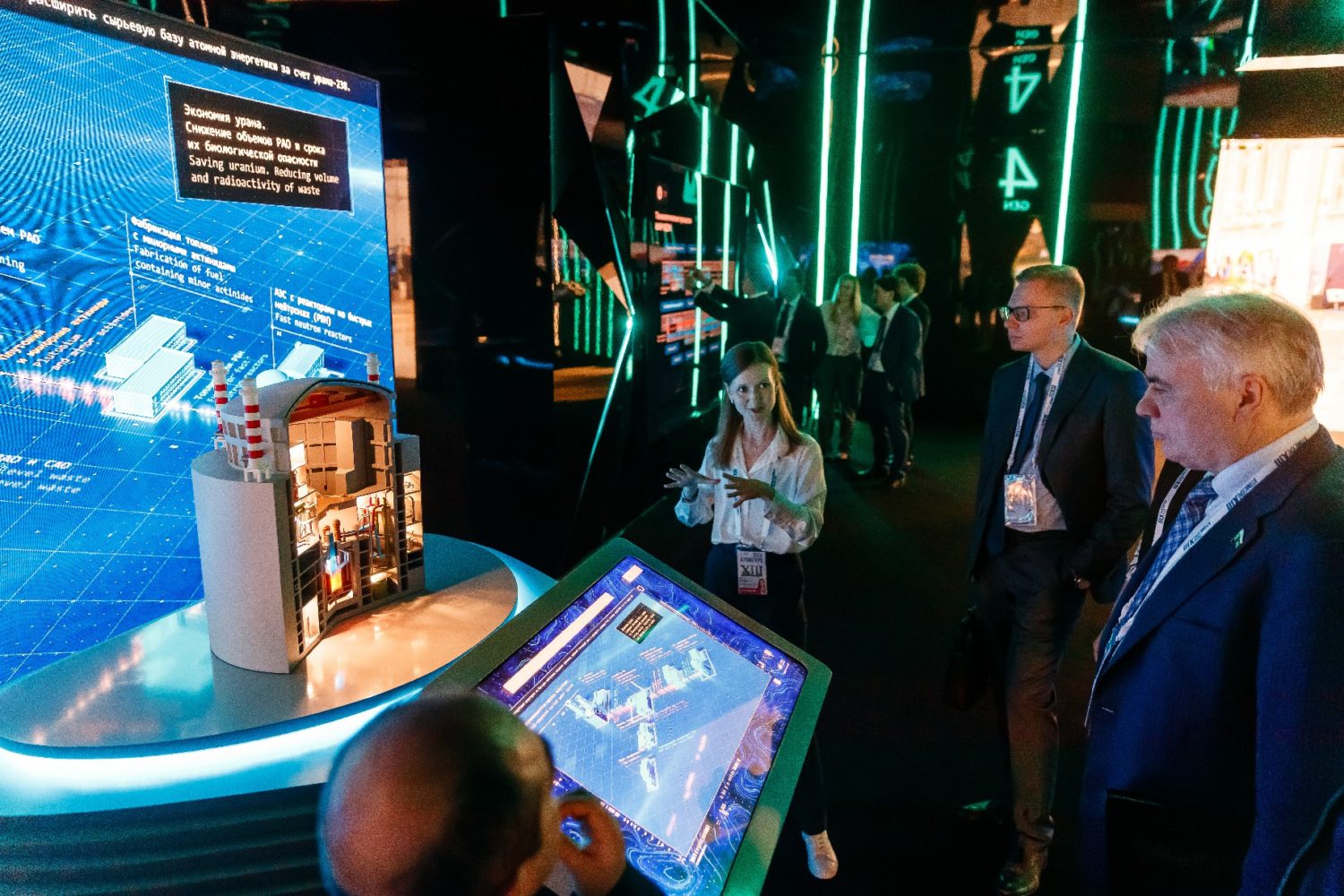
Systemic Approach to Generation IV
back to contentsThe global nuclear industry is trending towards a fundamentally new paradigm of reactor technology, which is referred to as technology of the fourth generation. But what does this concept hide? Russian nuclear engineers offer their own approach.
Speaking at the Atomexpo 2024 forum, Alexander Lokshin, First Deputy Director General for New Nuclear Energy Products at Rosatom, pointed out that the Generation IV concept was more about a complex system than just a reactor. He stressed that Generation IV systems were designed to solve two tasks, reprocessing of spent nuclear fuel and maximizing the use of natural uranium. At present, however, reactor fuel is made of uranium enriched up to 5 % U‑235. The share of this isotope in natural uranium is as little as 0.7 %, so most of uranium‑238 is stockpiled.
INPRO and Generation IV Forum
There is no single definition of what Generation IV is. The IAEA altogether avoids grading reactors by generation, having introduced the concepts of ‘innovative’ and ‘advanced’ reactors. However, the term ‘generation’ has taken root in the nuclear discourse worldwide and continues to be broadly used by the professional community. For them, Generations I, II, III and III+ differ in terms of safety (see the Reactor Evolution section below). As an example, Russian-designed VVER‑1200 reactors, which Rosatom is building around the world, belong to Generation III+ and are by far the safest.
It was Russia that initiated the current discussion on what kind of nuclear power the future needs. The discussion is ongoing within the framework of the International Project on Innovative Nuclear Reactors and Fuel Cycles (INPRO) launched in 2000 under the auspices of the IAEA. “The interest in the project was immense. Many developing countries, potential consumers of nuclear power technologies, including India and China, even anti-nuclear Germany, not to mention such countries as France or Japan, which dreamed of maintaining their existing reactor fleet, got involved right away,” former IAEA representative Vladimir Kagramanyan recalled in an interview with AtomInfo.ru.
From the very beginning, INPRO laid down the requirements for Generation IV systems — safety, non-proliferation, and waste management — that remain relevant today. “Russia had a conventional point of view. Spent nuclear fuel is not waste, but feedstock for fresh fuel within a closed nuclear fuel cycle that involves fast reactors,” Vladimir Kagramanyan said.
The next year came the Generation IV International Forum (GIF IV) initiated by the US. According to Vladimir Kagramanyan, it was supposed that Western developers would choose one or two technologies and build a demonstration reactor. However, it was discovered almost immediately that the approaches of the parties were too different, and so were their technologies. After all the discussions held, the parties agreed on a list of six Generation IV reactor technologies (see below) that meet their requirements. Admittedly, similar technologies are also being considered by INPRO.
“The studies conducted under INPRO have given the IAEA and the entire nuclear community reliable tools for evaluating nuclear energy as complex ‘long-lived’ systems aimed at sustainable development of mankind,” former IAEA Deputy Director General Alexander Bychkov said in an interview with AtomInfo.ru.
Both INPRO and GIF IV were guided by a set of similar criteria when defining the technologies of the future: these technologies should ensure continuous power generation with minimal waste; the cost of power generated should be lower compared to other energy sources over the entire service life; the level of their safety should exclude beyond design basis accidents; and non-proliferation should be guaranteed.
Purpose of the new systems
The need for fundamentally new nuclear technologies stems from three disadvantages of the existing water-cooled reactor designs. First, they operate with a relatively low efficiency. Second, they have high pressure in the primary circuit, which is potentially dangerous. And, finally, they use the thermal spectrum of neutrons, i. e., only a small portion of the energy potential hidden in natural uranium. So, the purpose of the new generation systems is to eliminate these drawbacks.
As IAEA representative Vladimir Kriventsev noted at Atomexpo 2024, each new technology (of those considered by GIF IV) has one or another disadvantage. For example, supercritical reactors have higher temperature and efficiency but also much higher pressure. In high-temperature gas-cooled reactors, the efficiency problem is solved, and high pressure is not that dangerous because they use gas as coolant, but the neutron spectrum is still thermal. Sodium-cooled fast reactors have none of the above drawbacks, but sodium reacts violently with water and air, so they need an intermediate (third) circuit. Lead-cooled fast reactors do not have this problem and feature higher safety compared to all other reactor designs, but there are increased requirements for structural materials, which must not be damaged by coolant or radiation. In addition, many of the technologies considered by GIF IV have not been tried or tested yet.
The approach followed by the Russian nuclear industry removes the question of ‘what makes untested Generation IV technologies be considered better than time-proven Generation III technologies’. Generation IV should include systems that have improved properties, such as safety, zero waste, cost effectiveness, and maximum use of raw materials, i. e., ensure more sustainability throughout the service life of a nuclear power plant.
Entering Generation IV
Russia focuses on complex systems and not on individual reactor designs (the latter is often the case worldwide). Along with new reactor concepts, Russian engineers concentrate their efforts on new types of fuel and fabrication technology and, most importantly, new approaches to what should be included in a nuclear generation facility, which can be viewed more broadly than just a nuclear station.
These ideas have most fully taken shape under the Proryv (Russian for ‘breakthrough’) innovation project carried out by Rosatom. The project provides for the construction of an experimental power generation facility in the premises of the Siberian Chemical Plant (part of Rosatom’s fuel division). The facility (called ODEK in Russian) will consist of an experimental lead-cooled fast reactor BREST-OD‑300, a fuel fabrication/refabrication unit, and a spent fuel processing unit. This combination will enable the testing of the first-ever cycle for the on-site reprocessing of spent nuclear fuel into fresh fuel. In other words, the problems mentioned by Alexander Lokshin will be solved in practice.
“The requirements for Generation IV reactors largely coincide with the objectives of the Proryv Project — closing of the nuclear fuel cycle, no need for evacuation and resettlement outside the plant site in case of an accident, and so on. These objectives of Proryv, which was not then called that, crystallized from the experience gained by the global and Soviet nuclear power industries in the late 1980s, and matured in the 1990s; the approaches of the Generation IV International Forum were established in the 2000s. So, the ideas were hovering around the world and evolved into approximately the same requirements, which we are implementing now,” Vadim Lemekhov, Chief Designer of the Proryv Project, told the Novy Atomny Ekspert (New Nuclear Expert) magazine.
The Proryv Project shows rapid progress. In mid-April, the Russian watchdog Rostechnadzor granted the Siberian Chemical Plant an operating license for the nuclear installations of the dense fuel fabrication/refabrication unit. Nuclear installations include any industrial facilities that produce, process or handle radioactive or fissile materials. Obtaining the license from Rostechnadzor allows proceeding to the next stage of equipment testing and production trials. At this stage, the entire production line for BREST-OD‑300 fuel assemblies will be run in a test mode. In late March, a carbothermal synthesis line was test-launched at the fuel fabrication/refabrication unit, and all Atomexpo 2024 visitors could watch the live broadcast of the launch.
In mid-April, an intermediate section of the reactor protective structure was sunk into the BREST-OD‑300 reactor pit, marking the completion of the second stage of its construction. The upper section is planned to be placed into the reactor pit this December. The final height of the structure will be 17 meters.
The entire ODEK is expected to be put in operation in 2030. Anyway, the research findings and engineering solutions used in it are already employed to design a commercial energy facility (CEF) that will include two lead-cooled fast neutron reactors BR‑1200. The CEF may also include an on-site spent fuel reprocessing and fabrication unit. The CEF should be competitive with other types of generation facilities.
Sodium-cooled fast neutron reactors contribute to the same overarching goals of closing the nuclear fuel cycle through spent nuclear fuel reprocessing, more fully exploiting the energy potential of natural uranium, and achieving higher cost efficiency. At the Beloyarsk NPP, the sodium-cooled BN‑800 reactor has been operating for the second year entirely on MOX fuel made from depleted uranium and plutonium extracted from spent nuclear fuel. Work is underway to design a sodium-cooled fast reactor BN‑1200. The site for the new reactor has been selected, and public hearings on the matter have been held. The goal for 2026 is to obtain a construction license. The first concrete is scheduled to be poured in 2027. The plan for 2031 is to obtain an operating license, bring the reactor to criticality and then to power.
Rosatom is also developing the molten salt reactor technology, which is also aimed at closing the nuclear fuel cycle and reprocessing spent nuclear fuel. Molten salt reactors are capable of burning minor actinides, which are highly radioactive elements emerging in nuclear fuel during irradiation in the reactor core. Removing minor actinides will significantly reduce the radioactivity of spent nuclear fuel.
The list of new technologies developed by Rosatom would be incomplete without mentioning high-temperature gas-cooled reactors designed to operate in combination with a hydrogen plant, spectral shift control reactors, and supercritical water reactors.
Indeed, Russia is not the only country in the world to be working on the future of nuclear energy as China and India are engaged in similar research, and attempts are made in other countries as well. However, the sophistication of sodium- and lead-cooled fast reactor technology, different fuels for the closed nuclear fuel cycle and many other solutions allows Russia to turn ideas into reality right now, making the global nuclear power industry more sustainable in terms of efficiency, rational use of raw materials and waste minimization.
GIF IV technologies
- Supercritical water-cooled reactor (SCWR)
- Sodium-cooled fast reactor (SFR)
- Lead-cooled fast reactor (LFR)
- Molten salt reactor (MSR)
- Gas-cooled fast reactor (GFR)
- Very high temperature reactor (VHTR)
Reactor evolution
Generation I. 1950–1960s. Early designs of power reactors fueled by natural or low-enriched uranium, moderated by graphite, light water or heavy water, and cooled by water or gas (CO2).
Generation II. Early 1970s — late 1990s. Light-water reactors: boiling water reactors (BWR) and pressurized water reactors (PWR, VVER).
Generation II+. This term sometimes refers to upgraded Generation II reactors built after 2000.
Generation III. The reactors of this class are characterized by a higher fuel and thermal efficiency, substantial safety improvements (including improved nuclear safety), and standardized designs.
Generation III+. These are improved safety reactors characterized by modular design, increased equipment unification, an ability to withstand a plane crash, and numerous passive safety systems (passive heat removal, core catchers, RPV cooling, etc.).