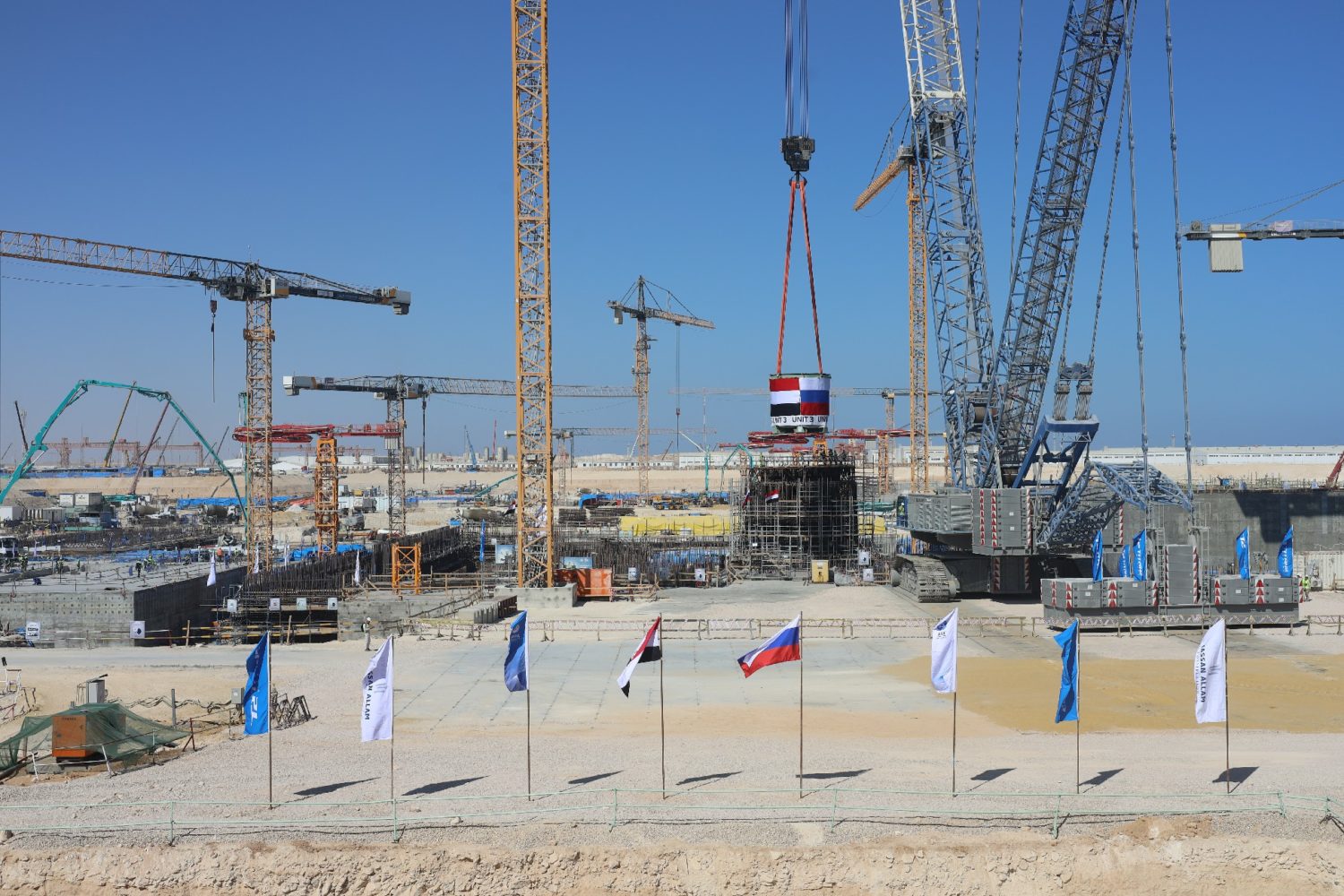
Safety as Top Priority
back to contentsIn early October, the installation of a core melt trap, also known as a core catcher, began at El Dabaa Unit 3 under construction in Egypt. This is one of this year’s milestones in the construction process.
Amged El-Wakeel, Chairman of the Board at the Egyptian Nuclear Power Plants Authority (NPPA), attended the ceremony.
“Egypt sees nuclear safety and security as a priority. The core melt trap belongs to the critical safety systems of El Dabaa NPP, which testifies to the highest level of nuclear safety and reliability of the nuclear plant operation,” Amged El-Wakeel said.
The ‘core catcher’ was installed using a heavy crane with a lifting capacity of 2,000 tonnes. Alexey Kononenko, Vice President of ASE and Director of El Dabaa Construction Project, stressed that the installation had begun in full accordance with the schedule. “This would not have been possible without all-round cooperation between the Egyptian customer and the general contractor. I would like to express my deep gratitude to everyone who made efforts to achieve this milestone of our joint project,” Alexey Kononenko said.
The core melt trap is a long-lead piece of equipment. It consists of several components weighing a total of 480 tonnes (its body alone weighs 155 tonnes). The cargo with the core catcher components was delivered to the seaport of the El Dabaa construction site in mid-summer.
In late September, El Dabaa Unit 2 entered another important phase as workers started erecting an inner containment shell (ICS) of the reactor building. The ICS erection is a complex multistage process that lasts about 15 hours and involves a heavy crane with a lifting capacity of 1,350 tonnes.
“Installing the inner containment shell is a labor-intensive process, which underlies safe operation of the nuclear power plant in the future,” Alexey Kononenko noted.
The inner containment shell consists of six tiers, the first of which includes 12 pre-assembled structural sections. The weight of each section ranges from 60 to 80 tonnes. The sections are manufactured at the El Dabaa construction yard by a subcontractor.
From Russia to Egypt
Russian nuclear companies continue to manufacture the necessary equipment for the Egyptian nuclear power plant.
In late September, Atommash, a Volgodonsk-based production facility of Rosatom’s mechanical engineering division, proceeded with manufacturing a reactor pressure vessel (RPV) for El Dabaa Unit 2. Steel billets for the RPV were cast at the St. Petersburg-based metallurgical plant of the mechanical engineering division and delivered to the production site in Volgodonsk. This is where the RPV parts will be assembled together.
Meanwhile, the work is going on to manufacture reactor equipment for El Dabaa Unit 1.
PetrozavodskMash, a mechanical engineering plant in Karelia, is manufacturing casings for the reactor coolant pumps that ensure coolant circulation in the reactor’s primary circuit. In addition to the pump casings, the plant will manufacture clad pipes, primary coolant pipeline assemblies, and a pressurizer.
In total, the production sites of Rosatom’s mechanical engineering division will manufacture and ship about 12,500 tonnes of different products for El Dabaa. This includes nuclear reactors with internals and heads, sets of steam generators, reactor coolant pump casings, primary coolant pipes, active and passive safety systems, and pressurizers.
On September 28, Russia celebrated the Nuclear Industry Workers’ Day. On the eve of the professional holiday of nuclear workers, steelmakers of AEM SpetsStal (part of Rosatom’s mechanical engineering division) cast the ‘first’ steel for the reactor pressure vessel of El Dabaa Unit 4. They made 192 tonnes of steel that will be used to manufacture a part of the VVER‑1200 reactor pressure vessel. The steel was produced in a powerful furnace that is capable of smelting 120 tonnes of metal in 2–3 hours. After casting, the steel was sent for out-of-furnace treatment and then to a vacuum chamber, in which it spent two days to cool down to 550–650 degrees Celsius.