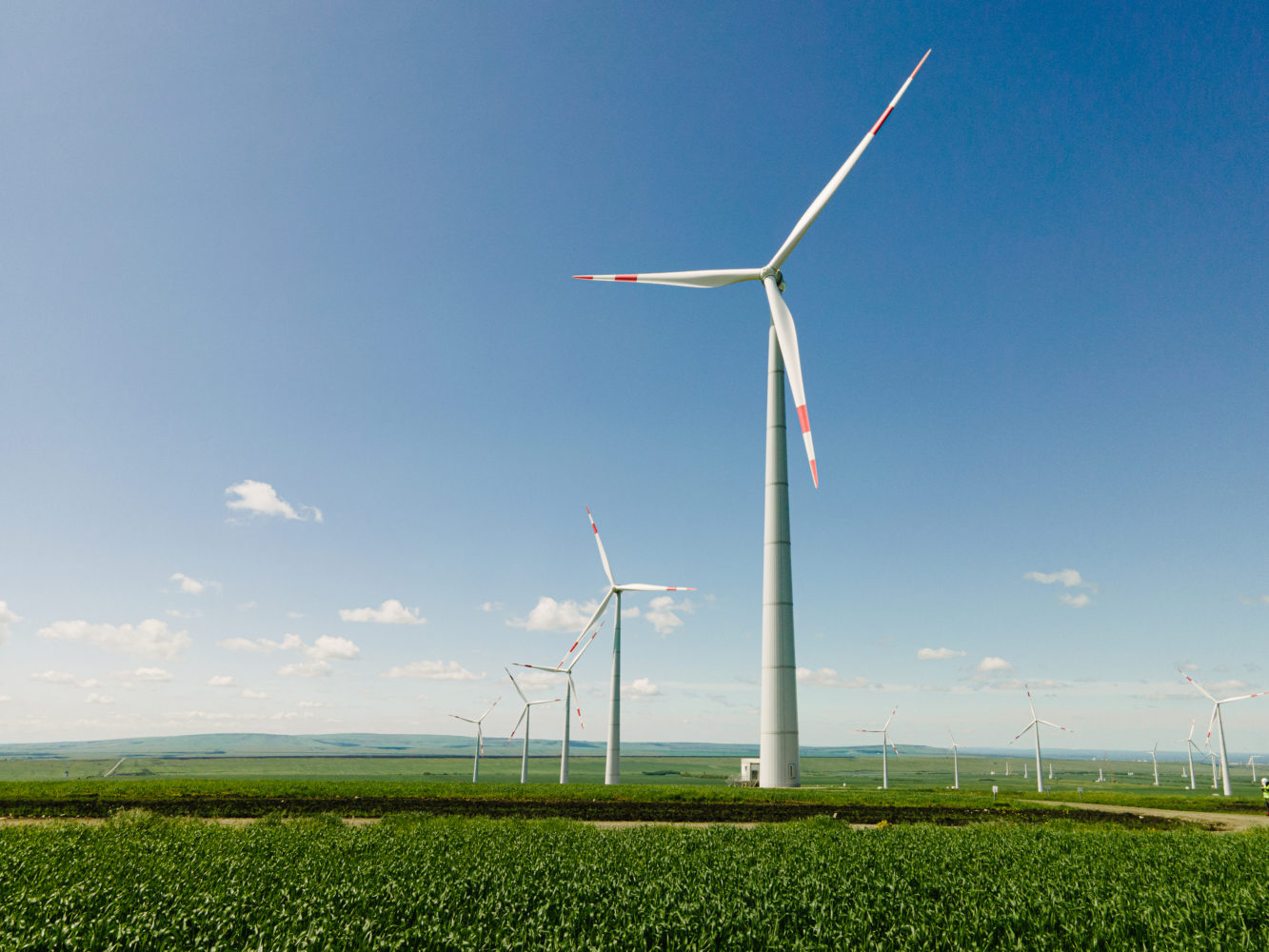
Blades Set Spinning
back to contentsThe first wind turbine was installed in mid-January at the Novolakskaya Wind Farm, which is being built by Rosatom’s wind power division, Rosatom Renewable Energy. It is 150 meters high and has 50 meters long blades. The wind farm is yet another move made by Rosatom to boost wind power generation in Russia. The Russian corporation also intends to build wind farms abroad, with in-house manufactured components, generators and blades, to be used in the construction.
The Novolakskaya Wind Farm is planned to have 120 wind turbines with a total capacity of 300 MW. The construction project will be divided in two stages, with 61 wind turbines to be installed in 2025 and another 59 in 2026. The wind farm is expected to generate 879 million kWh of electricity on the annual average. “I am confident that the Novolakskaya Wind Farm will make a large contribution to the efficient operation of the regional energy sector, securing economic stability and well-being of Dagestan residents,” said Grigory Nazarov, CEO of Rosatom Renewable Energy.
Taking into account the wind capacity commissioned to date, the wind power division of the Russian nuclear corporation will build 1.7 GW of new capacity by 2027.
1.7 GW
of wind capacity will be operated by Rosatom by 2027
Rosatom is also working on international wind power projects. Its program provides for up to 5 GW of renewable energy projects to be contracted by 2030. The key destinations for the program are CIS countries, Turkey, and others.
In March 2024, Rosatom and Kyrgyzstan signed an agreement at Atomexpo to build a total of up to 1 GW of wind capacity in the country. A 100 MW wind farm in the Issyk-Kul region of Kyrgyzstan is Rosatom’s first wind power project abroad. In September 2024, a memory capsule was laid at the planned wind farm site; in December, Rosatom Renewable Energy and the Government of the Kyrgyz Republic signed a project investment agreement. Site surveying and equipment ordering are scheduled to start in the second half of 2025.
Afterwards, the parties plan to assess other sites for the deployment of up to 900 MW of renewable capacity.
Self-reliance
It is important to mention that Rosatom builds wind farms with the components that are manufactured at the Rosatom Renewable Energy plant in Volgodonsk, Russia. Until recently, these included nacelles, hubs, generators, and tower base platforms only. Last December, the product range was added with blades, a key component of the wind turbine. Blades used to be imported, but now they are manufactured at a production site in Ulyanovsk, Russia, which is part of Rosatom’s composite division. These blades will be installed on the wind turbines of the Novolakskaya Wind Farm, and also be available to foreign customers.
“We have a number of international contracts, primarily in Kyrgyzstan, a member state of the Eurasian Economic Union, where our partners are looking for wind power technology to become technologically sovereign in this field. We will be glad to ship blades for their wind farms. A number of other countries are contemplating to build not only nuclear power plants but also ‘green’ energy clusters that will include wind and solar generation facilities,” said Rosatom Director General Alexey Likhachev at the opening ceremony for the Ulyanovsk plant.
Wind turbine blades are manufactured as follows. First, fiberglass fabrics are cut into pieces on a cutting table, with pieces then twisted into rolls. Spar caps are produced in parallel. A spar cap is a laminated strip running along the entire length of the blade half and consisting of several layers of carbon fiber fabric.
Then the blade halves are formed: fiberglass fabric, spar caps, and fastening elements for securing the blade to the generator hub (nacelle) are placed into the mold, followed by meshes, tubes and other parts. The mold is covered with film, vacuumed and filled with resin; then the halves are left to cure. Spars and lightning protection systems are installed onto the spar caps of the finished blade halves, which are then fitted together and glued. The seam quality is checked with a flaw detector and a thermographic camera. After the blade is assembled, blade mounting bushings are milled, glue seams laminated, and geometric parameters checked. The blades are then coated with putty, painted, weighed, balanced and sent to the finished product warehouse.
The design of the blade was commissioned by the wind power division back in 2016. The 51 meters long blade weighs 8.5 tons and is 90% glass composite and 10% carbon composite. The blades of this design are installed on 2.5 MW turbines produced by Rosatom Renewable Energy. Fiberglass and carbon fiber fabrics used in the blades are manufactured at a plant of Rosatom’s composite division. The plant is capable of producing 450 blades per year. The blades have been tested to international standards at a certification center.
Photo by: Rosatom Renewable Energy/ Newspaper Strana Rosatom