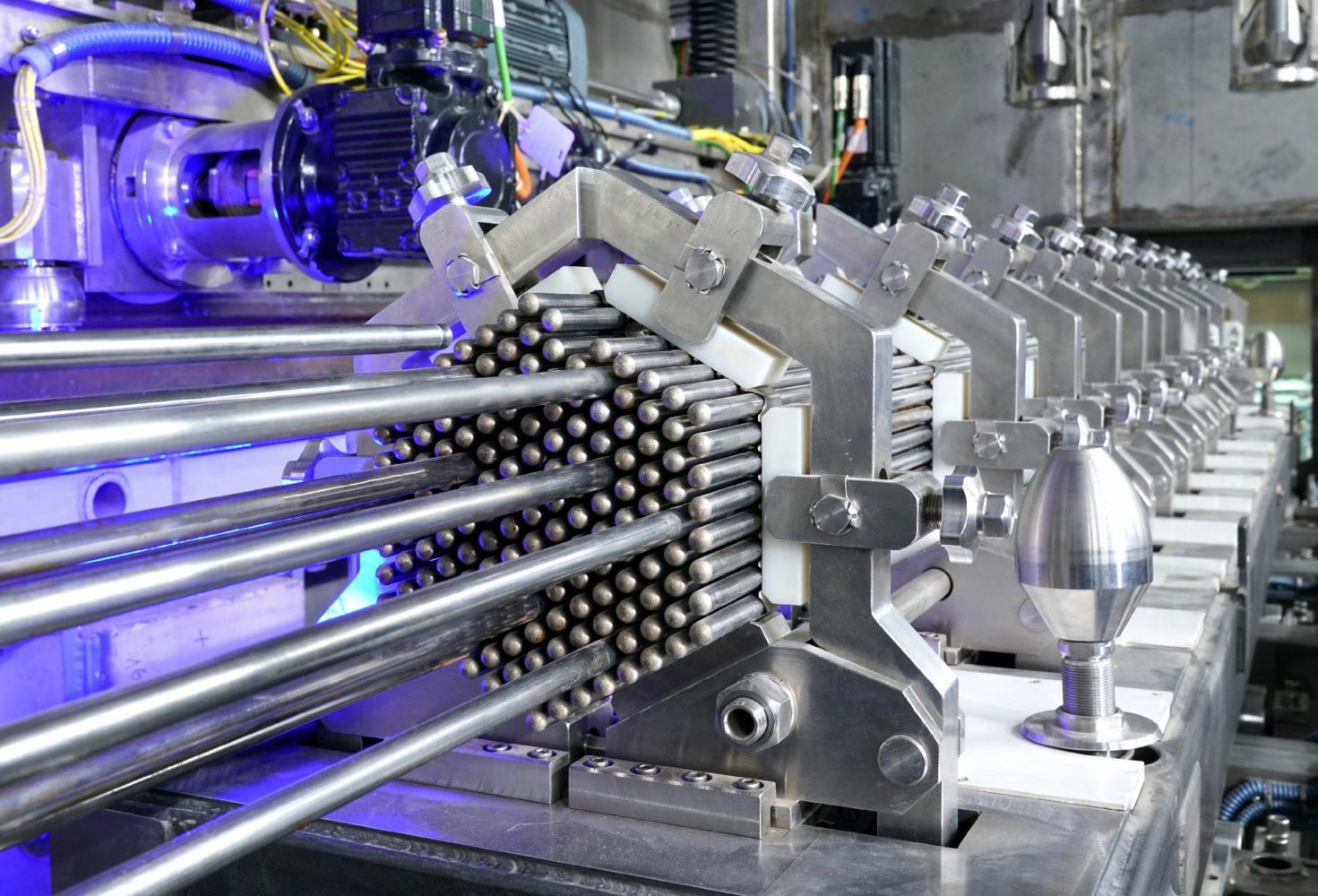
Fuel Expediting Future
back to contentsRosatom researchers and engineers have obtained impressive results in the development of advanced nuclear fuels. MOX fuel rods for VVER reactors successfully passed the second round of in-pile tests. A nuclear fuel fabrication/refabrication module for the BREST-OD-300 reactor was put into trial operation. Fuel for high-temperature gas-cooled reactors (HTGR) passed the first phase of testing. Read our article for details.
Fuel for BREST
The fabrication/refabrication module (FRM) was commissioned at the very end of December 2024. It is the first of three facilities being built at the Siberian Chemical Plant site for a Generation IV experimental power plant (abbreviated ODEK in Russian) as part of the Proryv (Breakthrough) Project.
Four process lines were launched at the FRM: carbothermal synthesis of mixed uranium and plutonium nitrides, fabrication of fuel pellets, production of fuel rods, and assembly of fuel bundles. The module is fully automated.
The FRM is designed to pilot the fabrication technology for nuclear fuel assemblies containing depleted uranium nitride. For now, only dummy fuel assemblies have been manufactured, but as soon as the Russian regulator Rostechnadzor approves plutonium manipulations, the FRM will begin manufacturing mixed uranium-plutonium nitride (MUPN) fuel. The lead-cooled fast neutron reactor BREST-OD-300 will need more than 200 MUPN fuel assemblies for the initial core loading. Earlier, experimental fuel rods containing MUPN fuel were tested in the BOR-60 research reactor and the BN-600 fast reactor.
ODEK is the world’s first attempt at building a Generation IV nuclear power system that includes a fast neutron reactor and on-site facilities for reprocessing irradiated fuel into fresh fuel. Generation IV systems imply a sharp reduction in waste and a fuller use of natural uranium by closing the nuclear fuel cycle. Rosatom has advanced furthest in the world in developing such systems.
In February, Rosatom’s production site in Glazov began manufacturing round and hexagonal stainless steel tubes for the BREST-OD-300 core. They will be used to make fuel assemblies, reflectors, and shields. The new production line comprises nearly 30 machines and other pieces of equipment. “We plan to finish the first batch of high-tech tubes in the coming months,” said Sergey Chineykin, CEO of the plant.
MOX fuel for VVER reactors
Mixed oxide (MOX) fuel passed the second round of in-pile tests in the MIR.M1 research reactor. Their results showed that the nuclear fuel reached the planned burnup level with fuel rods remaining sealed. It is planned to hold a total of six test rounds under different conditions, including normal operation, emergencies, and design basis accidents.
A batch of MOX fuel rods is also being tested at the critical test facility BFS-1. Test results will be used in a feasibility study for the core of the advanced VVER‑S reactor (S in its name stands for ‘spectral shift control’). MOX fuel is expected to improve fuel economics, reduce accumulated stockpiles of depleted uranium, and facilitate flexible use of regenerated materials.
It is planned that a nuclear station with a VVER‑S reactor will be the first in the world to have a light-water reactor fully loaded with MOX fuel assemblies.
HTGR fuel
In late December 2024, Rosatom researchers completed the first phase of in-pile tests on laboratory samples of HTGR fuel under extremely high temperature conditions. First, the fuel was kept for more than 400 effective days at a temperature of 1,000–1,200 ℃. Then it was irradiated for 500 hours at a temperature of 1,600 ℃. The results show that the multilayer coating of tri-structural isotropic (TRISO) fuel particles is perfectly capable of retaining gases produced inside them, even when subjected to high temperatures and radiation. The second testing phase scheduled for this year provides for tests at extreme temperatures of up to 1800 °C.
In January, Rosatom completed a three-year equipment development program for the pilot HTGR fuel production line. Engineers developed detailed specifications for the manufacturing technology, including equipment, production processes, and key operations. The pilot line consists of four process sections equipped with Russian-designed machines. For example, a domestic X-ray CT scanner is used for the online control of fuel particle distribution in the fuel compact.
The pilot fuel line is designed to manufacture 250,000 fuel compacts per year, securing fuel supply for the yet-to-be-built nuclear power plant. It is planned that it will consist of a high-temperature gas-cooled reactor and a chemical facility manufacturing hydrogen-containing products.
Photo by: JSC “SKHK”, JSC “Scientific Research Institute NPO “LUCH”