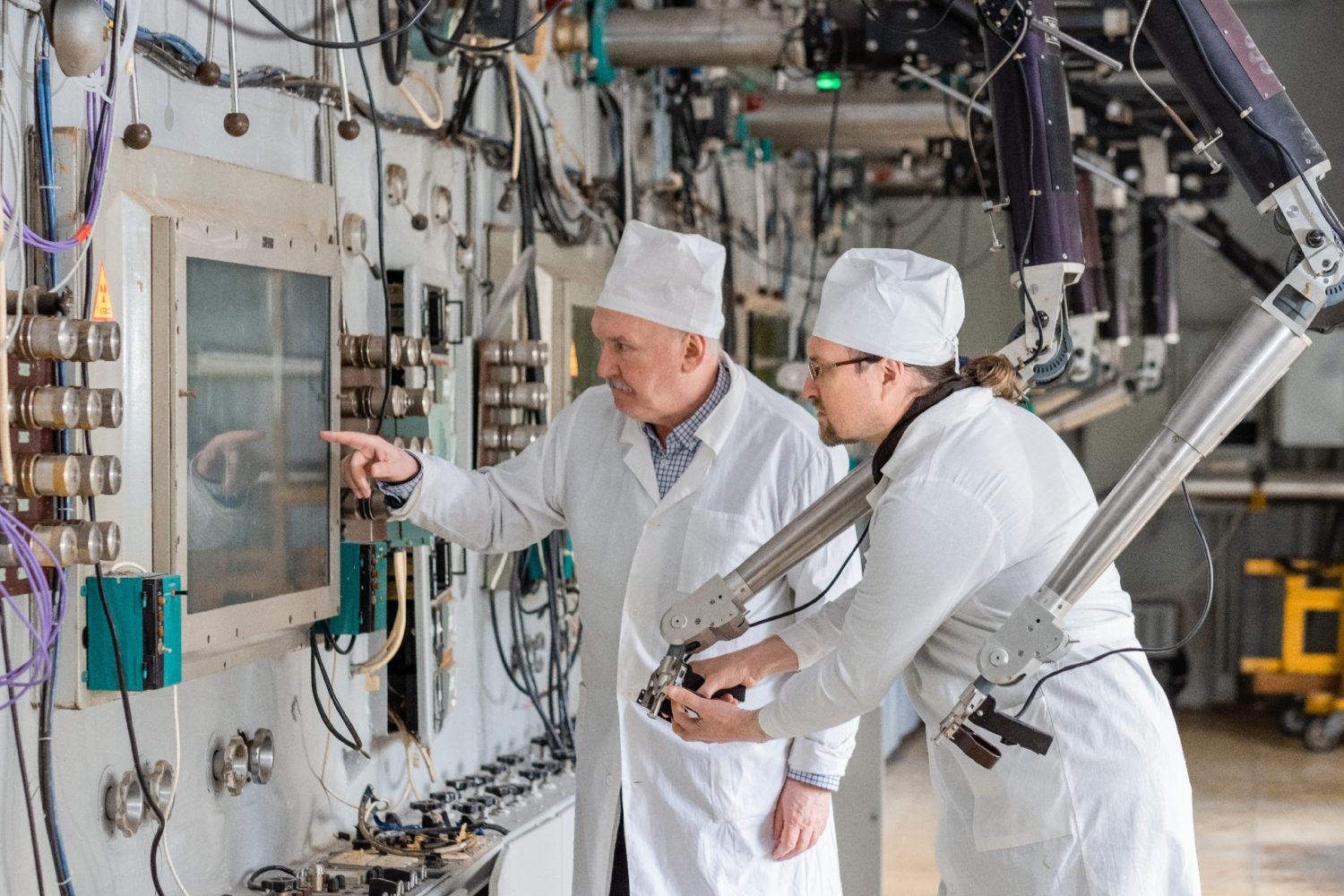
Liquid Salt Destroys Minor Actinides
back to contentsIn December 2022, N. Dollezhal Research and Development Institute (NIKIET, part of Rosatom) presented a draft design for a molten salt research reactor (MSRR). The new reactor is designed as a test facility to validate technologies for a full-scale minor actinide burner.
Purpose and principles of operation
In molten salt reactors, nuclear fuel is dissolved in a metal fluoride salt medium, which also serves as a coolant, with a salt-and-fuel mixture forming a homogeneous reactor core.
Molten fuel salt reactors have a number of distinct advantages. First, unlike heterogeneous reactors, they need no fuel rods or fuel assemblies.
Second, molten salt reactors are much safer due to negative reactivity feedback for both temperature and density of the fissile medium. And since their temperature and void coefficients are negative, no severe accident can ever happen. The pressure in the fuel circuit is low but sufficient to pump the molten salt medium through. This minimizes the amount of potential energy that can be released if the circuit is damaged or broken. And if the temperature in the circuit rises to a dangerous level, a relief valve triggers, whose passive action is based on natural laws of physics.
The main purpose of a molten salt reactor is to enable continuous transmutation – or ‘burning’ – of minor actinides contained in spent nuclear fuel from thermal neutron reactors. Since molten salt reactors make it possible, Russia has returned to this concept after a long break (research activities into molten salt reactors were suspended in Russia in the early 1990s). Molten salt reactors are now seen as part of a closed nuclear fuel cycle and an important component of the spent nuclear fuel reprocessing and disposal technology.
The MSRR is planned to be built on the premises of the Mining and Chemical Plant (MCP, part of Rosatom) in the Krasnoyarsk Krai. The choice is not accidental since MCP specializes in the final stage of spent nuclear fuel management and nuclear decommissioning.
MSRR project timeline
Engineering studies and computations for the MSRR began in late 2019. By now, the R&D program for the project has been approved and, as part of this program, feasibility studies have been launched into MSRR structural materials, reactor unit, spent fuel reprocessing module and other equipment, as well as into the technology for the preparation of fuel and flushing salts and other processes. “We are now working to make unparalleled high-temperature test benches to refine technical solutions for certain assemblies and verify software codes for this innovative reactor unit,” says Igor Tretyakov, Chief Designer of Research and Isotope Reactors at NIKIET.
As part of the draft design, engineers developed basic technical, structural, schematic and layout solutions for the reactor unit and the equipment it will contain. Much of front-end engineering is still ahead, including justification of investments, development of the detailed design for the reactor and reprocessing module, completion of the R&D program, and, finally, development of detailed technical documents and licensing. MCP plans to be licensed as an MSRR site later this year. “This means that a substantial portion of R&D feasibility studies should be done before 2024,” Igor Tretyakov explains. It is planned that MCP will obtain a construction license by 2027, and the MSRR will be constructed by 2031.
MSRR specific features
The MSRR has a thermal capacity of 10 MW. Its primary structural material will be an alloy containing 80% of nickel. It is planned that this alloy will be used to make a reactor pressure vessel, pipes for the fuel (in more familiar terms, primary coolant) circuit, and thermal equipment. “Researchers have studied how this material reacts with the fuel salt and its corrosion behavior, and have chosen it for now – the deadline for the engineering design is very tight, so we have to go the shortest way. It is quite possible, though, that R&D results will push us into considering other materials and other salts,” Igor Tretyakov said.
It is assumed that around 10% of molten salt will be withdrawn from the fuel circuit at certain intervals, with a fresh fuel mixture added instead. Theoretically, it is not necessary to shut down the reactor for refueling, but this yet needs to be researched, analyzed and proved experimentally.
Presumably, the reactor will be built in the underground section of MCP. The rock massif will additionally isolate the reactor from the environment. Besides, the fuel circuit and some other pieces of equipment will be housed in a sealed box serving as a safety barrier.
In order to protect the personnel, most of the maintenance work on the MSRR is planned to be done with robotic mechanisms, which are also being developed now.
A few words about fuel
MSRR fuel and methods of its reprocessing are developed at A. Bochvar Russian Research Institute of Inorganic Materials (VNIINM, part of Rosatom). The MSRR will use molten fluorides of several metals as fuel. The fissile material in the melt will comprise fluorides of minor actinides to be transmuted, and obviously, plutonium at the initial stage of operation.
One of the tasks VNIINM is working on is the production technology for minor actinide fluorides. “The synthesis of fluorides is not particularly difficult – its methods have long been known. But in order to use these compounds as fuel in the MSRR, they should meet stringent technical requirements, primarily in terms of oxygen content,” VNIINM Chief Researcher Alexey Ananyev noted in an interview for Strana Rosatom corporate newspaper.
VNIINM plans to use lithium and beryllium fluorides as a base for the fuel composition. They are less reactive to structural materials than sodium, lithium and potassium fluorides (FLiNaK). Obtaining salts of the required quality is the second task of VNIINM.
Its third task is to remove tritium, which is formed from lithium during irradiation. VNIINM has already selected sorbents for tritium extraction and developed a draft design for a gas purification system; experiments are currently underway. Meanwhile, designers are developing process equipment for the fuel preparation and reprocessing modules and gas purification systems.
The work to build the MSRR and fuel reprocessing module is progressing, albeit not without difficulties inherent in every new technology. The MSRR will be used to conduct experiments that will contribute to developing the technology for burning minor actinides from spent nuclear fuel, which will be a huge step forward to closing the nuclear fuel cycle.