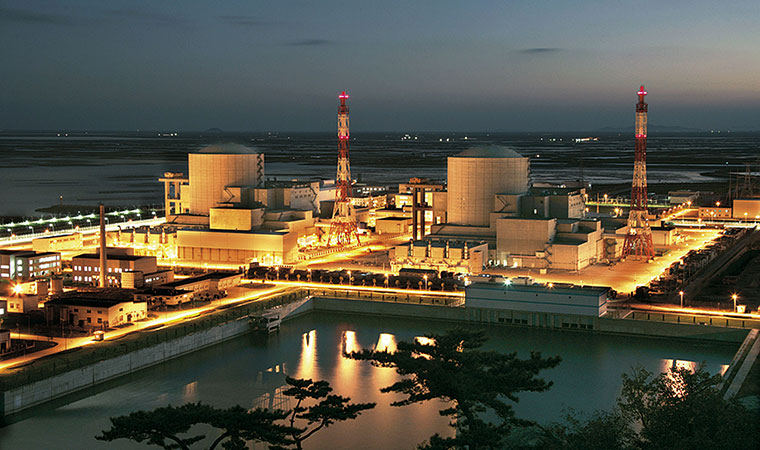
Repairs under Rosatom’s supervision
back to contentsA contract for assistance in the repairs at Tianwan NPP was made between Rusatom Service (a Rosatom Group company engaged in maintenance, repairs and upgrade of Russian-designed nuclear stations abroad) and Jiangsu Nuclear Power Corporation (China) for 2015–2017. Tianwan Unit 1 was brought offline in late February for a periodic overhaul to last 53 calendar days.
As part of its work scope, Rusatom Service will supervise equipment installation at Unit 1, modernize the first-circuit headers of steam generators No. 1 and No. 3 by replacing old gaskets and seals with thermally expanded graphite and assist in adjusting the position of protective tubes due to the adoption of TVS-2M nuclear fuel. The company will also repair circulation pumps and audit turbine blades.
The project will involve 15 Russian subcontractors, including Rosatom Group companies (Rosenergoatom, OKB Gidropress and the Central Design Bureau of Machine Building) and Rosatom’s long-standing partners (Power Machines, Kurchatov Institute and others).
As a company of Rosatom’s electric power division, Rusatom Service offers a comprehensive range of maintenance solutions and supplies to VVER-based nuclear stations outside Russia. It is present in almost all the countries with operational nuclear stations of this design and has leading positions in China, Iran, Bulgaria and Armenia where it acts as a general contractor in life extension, preventive maintenance and equipment upgrade projects at VVER-based nuclear stations. Its portfolio of international contracts approaches $500 million. “A major part of our portfolio accrues to the Armenian NPP life extension and modernization project totaling almost $300 million. Another major project – about $40 million – is maintenance and repair of the Bushehr NPP in Iran. Bulgaria’s Kozloduy NPP is another plant where we work on the service life extension and modernization of the generators at Units 5 and 6,” says Evgeny Salkov, CEO of Rusatom Service.
Rusatom Service and the Armenian NPP have signed a number of project documents, including a framework agreement, a project management contract, a due diligence contract and an equipment modernization and supply contract. The project comprises two stages. The first stage, an 18-month technical due diligence, consists of 16 individual audit programs. Its deliverable will be a service life extension and upgrade plan. Life extension as such will be the project’s second stage. As always, safety improvement will be an utmost priority.
The Iranian project of Rusatom Service includes two preventive maintenance repairs and an overhaul at Bushehr NPP Unit 1. “Iran is an emerging nuclear country, but they go ahead and study hard. We see that requirements for us as contractors become more stringent. On the other hand, the Iranians want to do a larger part of work on their own, and need guidance and support. This refers, for example, to spare parts and repairs. Our Iranian colleagues aim at planning and doing NPP maintenance and repairs independently.
Rusatom Services is involved in the modernization of Kozloduy NPP. The first project was focused on the upgrade of power generating equipment at Unit 6. The contract was signed in 2013. Despite a number of challenges, an unprecedented nature of the project and some issues that no one had foreseen, the project was a success. At present, all the equipment works as designed. The upgrade can boost the unit up to 104% of the rated capacity. Rusatom Service is providing repair services for the generating equipment at Kozloduy Unit 5. This project targets an increase in Unit 5 capacity up to 104% and the generator’s rated capacity up to 1,100 MW. For this purpose, the generator stator will be replaced with a new one while the rotor and exciter armature will be repaired at the manufacturing plant in Saint Petersburg. Rusatom Service and the manufacturer agreed to start the production before the contract was signed to meet the deadline set by the Bulgarian customer. The rotor and the armature have been shipped to the manufacturing plant in Saint Petersburg for repairs.