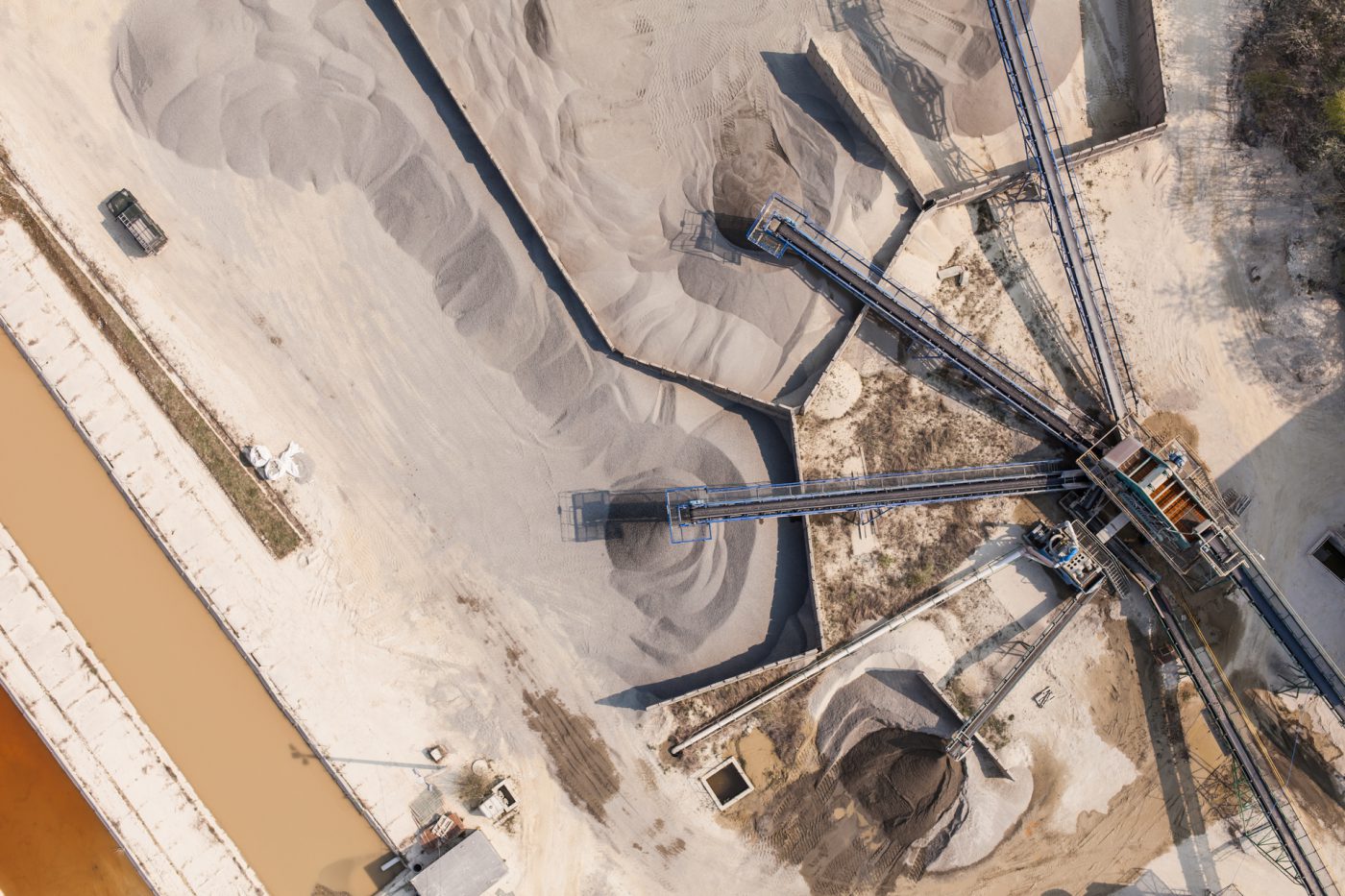
Australian Nickel Production to Benefit from Russian Uranium Technology
back to contentsVNIPI is an engineering subsidiary of ARMZ Uranium Holding, Rosatom’s mining division. The company provides design and engineering services for Clean TeQ’s nickel, cobalt and scandium leaching process at the Sunrise processing plant.
It was Clean TeQ’s initiative to contact VNIPI. Russian engineers working in the Australian company were well aware of VNIPI’s capabilities. They knew that VNIPI has long been providing design services for mining projects across former Soviet Union. Some of the projects involved the resin-in-pulp process that was of particular interest for the Australian company.
Resin in pulp
The ion exchange technology, which the resin-in-pulp process belongs to, has long been used for the extraction of uranium and precious metals (mostly gold) in former Soviet republics, primarily in Russia and Kazakhstan.
The essence of the resin-in-pulp technology is for the pulp and resin being fed into a series of reactors in a counter current manner. The pulp reacts chemically with the metal and absorbs it. Two processes – leaching and sorption – run in parallel, thus improving the recovery rate. After that, the barren pulp (“tailings”) goes to the waste dam, and the loaded resin goes to desorption. The metal is recovered, and the desorbed resin returns into the sorption circuit.
There is a specific resin grade and a set of reactors for each metal. Each set of reactors extracts one metal only. A similar project with two sets of reactors – for uranium and molybdenum respectively – is developed at VNIPI for another subsidiary of Rosatom’s ARMZ Uranium Holding.
A distinctive feature of the Russian technology is that resin interacts directly with pulp. In other mining countries including Australia, pulp is first divided into liquids and solids, so that the sorption process uses pure solutions only. This technology is more expensive as it employs filtration and clarification equipment, which is costly and needs extra space at the processing plant. Additional expenses for electric power and repairs are also unavoidable.
Nickel is almost never recovered using the ion exchange technology. Examples are few. In 2002, a patent to use the resin-in-pulp process for cobalt and nickel extraction was obtained by BHP, the largest Anglo-Australian mining company. Another example is Anglovaal Mining from South Africa (now part of African Rainbow Minerals) that is piloting the resin-in-pulp technology to extract nickel, cobalt and copper. The technology for Anglovaal Mining was developed by local research company Mintek.
Experts are able to understand each other
The first step was to study the technology in detail. Australian engineers analyzed chemical and physical parameters of the process and specifications of the equipment. They wanted to calculate the exact parameters, such as the amount of feedstock supplied and concentrates obtained, recovery rate, process losses, operating parameters of the equipment, consumables and, finally, economics of the entire process, including production costs and labor productivity. Calculations were made separately for each metal.
Those difficulties arose because Russian and Australian engineers were using different data processing software programs. VNIPI experts managed to convince their Australian colleagues that their calculations were accurate. “Experts will always understand each other because it is a matter of mathematics,” Roman Kovalyov from VNIPI explained.
At present, engineers are discussing the shape of reactors for the resin-in-pulp process. Clean TeQ plans to install U-shaped columns, while Russian engineers propose using ordinary Pachuca tanks since they make the process more cost-efficient. The Pachuca tank is a barrel-like vessel with a cone-shaped bottom. It was named after an engineer who developed it.
Russian engineers were surprised by the meticulousness on the customer’s part. “When they come to Russia, we spend no less than a week discussing all the details. They are interested in equipment specifications, components, workmanship, column types, and so on. We have discussed mesh sizes and composition of the solutions,” Alexey Shemetov, CEO of VNIPI, says.
Last September, VNIPI submitted the first package of design documents for the leaching section of the plant. The customer accepted the documents and signed a contract for the next phase, which involves conducting a pre-feasibility study. This phase is planned to be completed by the end of 2020.
According to the definitive feasibility study of the Sunrise Project (as of 25 June 2018), the plant is expected to process 2.5 million tons of ore per annum for 25 years. The expected annual output of nickel sulfate will be 89,270 tons. The output of cobalt sulfate will be 21,260 tons per annum.
Clean TeQ is VNIPI’s first – and hopefully not the last – customer outside of the former Soviet Union. VNIPI plans to sign more contracts with external customers that do not belong to Rosatom Group. According to Alexey Shemetov, their share will grow to 70% of the order portfolio.
Clean TeQ, which is listed on the Australian Securities Exchange, is a reputable customer. Its shareholders include Robert Friedland, one of the most successful mining industry investors, and Chinese Pengxin International Group Limited (USD 1.3bn market cap). Success of the project will be the best recommendation of VNIPI for international customers and raise interest in the services of the Russian engineering company.
Sunrise in numbers
Plant capacity | 2.5 million tons of ore per annum |
Expected mine life | 25 years |
Project CAPEX | USD 1.49 billion |
Average production cost, incl. income from by-products | USD 1.46 per pound (key product is nickel) |
Average production cost, excl. income from by-products | USD 4.68 per pound (key product is nickel) |
Nickel sulfate output | 89,270 tons per annum |
Cobalt sulfate output | 21,260 tons per annum |
Scandium output | 250 tons over 25 years |
Average recovery rate (nickel) | 92.6% |
Average recovery rate (cobalt) | 91.2% |