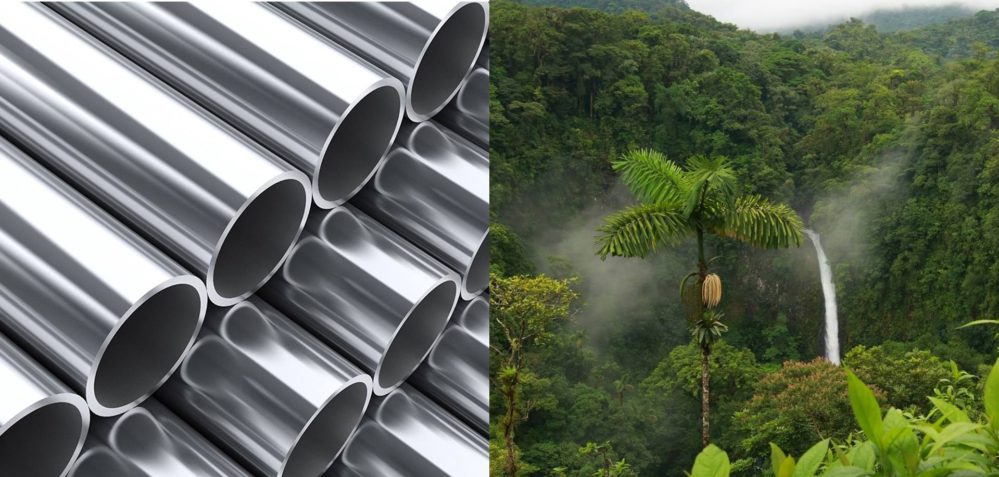
Rosatom Offers Super Steel
back to contentsTropical environments are known for heavy dews, chloride contaminated air, high temperature and humidity, which are all contributors to corrosion. However, the latest developments in the global nuclear power industry show that new nuclear power plants will mostly be located in tropical areas. Corrosion affects nuclear safety, which is well known to be a top priority for Russian nuclear engineers. Material scientists of the Central Research Institute for Machine Building Technology (a subsidiary of AEM Group) have developed a new steel alloy for tropical environments with excellent heat and humidity resistance properties.
The new steel alloy known as 08H14MF is designed to manufacture heat exchange tubes of passive heat removal systems (PHRS) that will be used in tropical conditions. The PHRS is one of the most important components of a nuclear power plant as it ensures safety of nuclear operations in emergencies. Passive heat removal systems have been installed at Kudankulam (India) and Novovoronezh-2 (Russia), and are provided for in the Akkuyu project (Turkey).
Due to the lack of experimental data on corrosion behavior in a tropical environment, the steel alloy needed test-supported proofs that it can be used in passive heat removal systems of nuclear reactors.
Climate resistance tests were carried out by the Central Research Institute for Machine Building Technology and OKB Gidropress (both belong to Rosatom’s engineering division AEM) and lasted half a year to cover all seasonal changes. Visual observation was used as a method to control the condition of the surface. No corrosion was detected on the steel surfaces of the heat exchanger, and tubes remained clear and shiny. The annual corrosion rate of the new steel alloy does not exceed 5.4 µm even in the harshest conditions (at the average salt spray accumulation rate of 600±75 mg/sq m per day). This means that corrosion will not exceed 0.3 mm in 60 years, or the entire service life of a PHRS. There is no doubt, therefore, that the steel alloy in question is highly resistant to environments with a low chloride content. Electrochemical tests have also shown that it demonstrates excellent resistance behavior in humid marine climates.
Ambitious goal
“The steel alloy 08H14MF was developed by material scientist Veniamin Borisov from the Central Research Institute for Machine Building Technology. The goal was ambitious as he wanted to develop a stainless steel alloy that was easily machined and perfect for making steam generator tubes. Ideally, it should contain no nickel, which is the most expensive of all alloy components,” said Ivan Safonov, PhD in Chemistry and Head of the Corrosion Test Laboratory, Central Research Institute for Machine Building Technology, in an interview to Rosatom Newsletter. “The material was tested many times for different uses ranging from rail car roofs to sinks.” According to Ivan Safonov, it was the wide range of applications in the past that helped this steel alloy enter the list of candidate materials for climate-specific heat removal systems.
“Of course, it is not perfect for extremely aggressive media, but well suited to humid climates. When we worked on the Kudankulam project, we developed a steel aluminizing technology – the PHRS made of the resulting material is still fully operational. Gidropress suggested using 08H14MF at the Akkuyu plant. A special software application was developed to model the PHRS service life with various corrosion testing methods. There was much work to be done, and we were lucky to have competent interns from the National University of Science and Technology. Each intern tested one system in three modes with a salt spray chamber and electrochemically. We summarized results in the final report, and the PHRS was approved,” Ivan Safonov said.