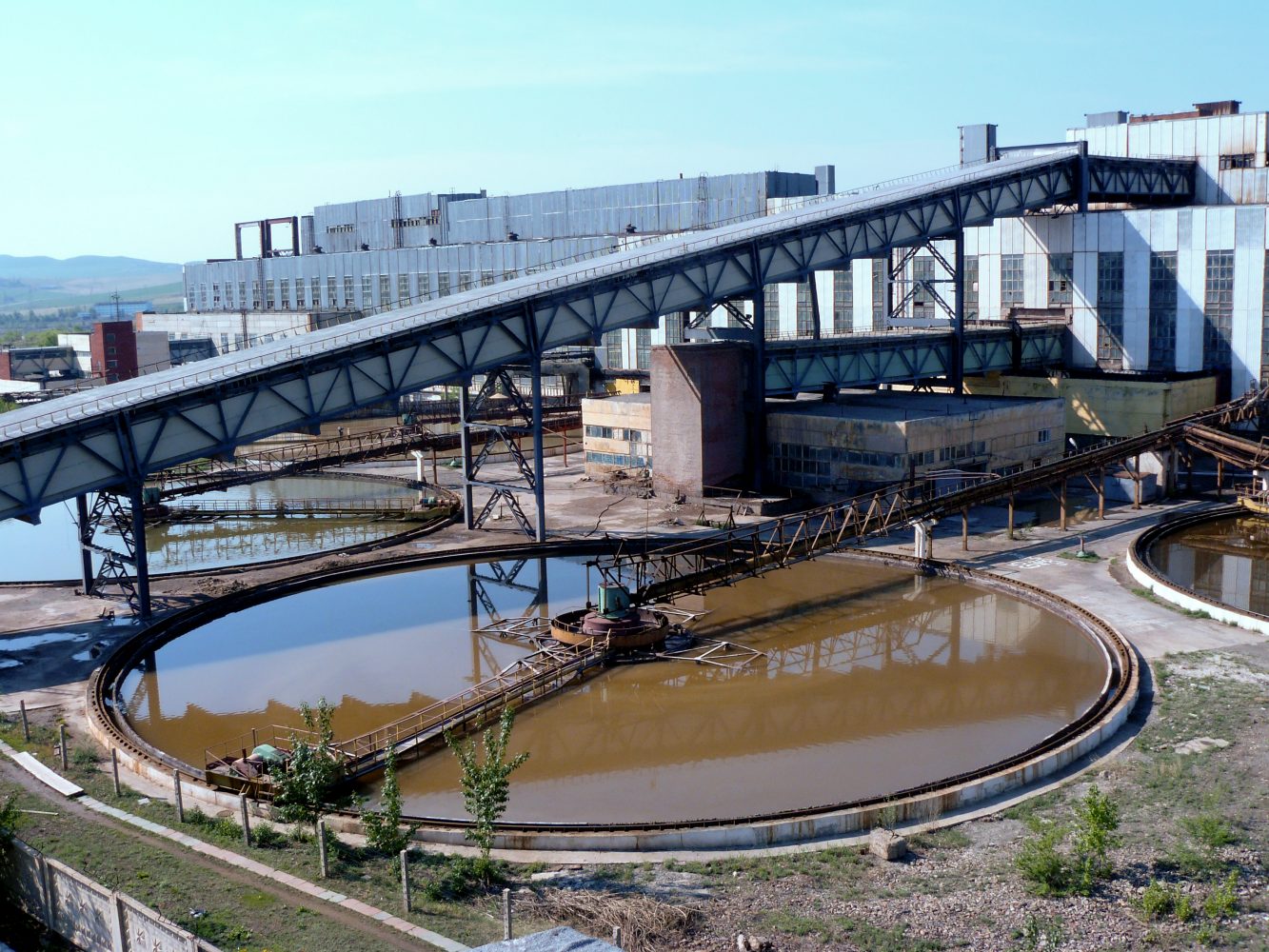
Mining Future Belongs to VNIPIpromtechnologii
back to contentsVNIPIpromtechnologii was established on 17 April 1951. Back then it was called State Construction and Design Institute No. 14. Its primary task was to design uranium ore mining and production facilities and other nuclear-linked mining plants.
Uranium deposits in the Soviet Union were discovered in the late 1940s in the Fergana Valley (present-day Tajikistan), near Kryvyi Rih (Ukraine), in Kyrgyzstan, Northwest Russia (particularly Chukotka), and Zabaykalsky Krai. The country needed to mine and process uranium ore and needed new facilities for this purpose.
Mining
The first production facilities designed by State Construction and Design Institute No. 14 were a mining plant and a hydro metallurgical plant at the Zhovti Vody deposit (Ukraine). The plants began mining uranium ore and producing uranium as soon as 1959. In what is now Uzbekistan, State Construction and Design Institute No. 14 designed production facilities for the Severnoye Mining Department at the Uchquduq deposit. In January 1959, the institute issued terms of reference for the development of the Uchquduq deposit. They provided for 11 open pits and 14 mine fields to combine open-surface and underground mining methods. The institute also designed a solvent-in-pulp uranium extraction process for the Lermontov Hydro Metallurgical Plant (Stavropol Krai). The institute also acted as a general designer for the Priargunsky Mining and Chemical Plant (now Priargunsky Industrial Mining and Chemical Union, part of Rosatom) at the Streltsovskoye deposit. In the 1960s, the institute was the first in the Soviet Union to develop an in-situ leaching process, which proved to be the most environmentally friendly and cost efficient. Over the years, VNIPIpromtechnologii designed nearly 70 mining plants and facilities.
Along with mining plants, it has designed auxiliary infrastructure, including mechanical repair shops, vehicle repair facilities, thermal power plants, boiler plants, internal and external utility systems, communication lines, automated storage facilities, and even towns and villages.
As the years went by, the institute extended the scope of its activities to go beyond nuclear-related minerals (uranium, beryllium, lithium, etc.). It started developing designs for gold and polymetallic ore mining and processing plants. One of them is Navoi Mining and Metallurgy Plant that produces gold from ores coming from the world’s largest gold deposits, including Muruntau, Pokrovskoye, Mnogovershinnoye, Udokan and Nezhdaninskoye.
At present, VNIPIpromtechnologii continues providing expert supervision services for domestic and foreign plants it has designed. For example, the institute designs upgrades and retrofits for the Navoi Mining and Metallurgy Plant (Uzbekistan). In 2018, Uzbekistan’s State Commission for Natural Reserves approved Muruntau reserve estimates prepared by the Navoi Mining and Metallurgy Plant on the basis of surveys conducted by VNIPIpromtechnologii. The institute developed a cost-efficient solution for the plant to develop small gold deposits located within 50 km around the Central Mining Administration. The development of these small deposits will enable the Navoi Plant to maintain a stable output of gold until 2120. The institute also designed a conveyor line intended to carry overburden to dumping grounds and a steep inclined conveyor with a carrying capacity of almost 10 million tonnes of ore per annum. In 2019, VNIPIpromtechnologii prepared a gold mining schedule for the Muruntau and Myutenbai deposits for a period until 2030. The technical solutions offered by the institute enables processing lower-grade ores. That same year, the institute developed a mining operations plan for the Muruntau deposit. In June 2020, VNIPIpromtechnologii offered optimal solutions for ore and rock flows and location of transportation conveyors.
Site rehabilitation
After the Comprehensive Nuclear-Test-Ban Treaty was signed, the institute turned to designing nuclear waste storage sites and developing solutions to deal with hazardous industrial waste. At present, VNIPIpromtechnologii continues working in this area. One of the recent examples is a land rehabilitation project in Karelia. The institute launched a site survey in May 2020 and plans to finish it in September. Its expected result is a zero possibility of radioactive contamination.
VNIPIpromtechnologii has developed rehabilitation programs for uranium tailing dumps located in the villages of Kadji Say and Min-Kush (Kyrgyzstan) and near the city of Taboshar (Tajikistan) as part of the Uranium Mining Site Rehabilitation Program for EAEU States Affected by Uranium Production. In North Ossetia, the institute helped the local company Pobedit to decommission its thoriated tungsten production facility. Its engineers develop individual waste management and safety solutions for each production facility.
New focus areas
Since 2010, VNIPIpromtechnologii has been part of Rosatom’s mining division ARMZ Uranium Holding and acted as an engineering center for mining applications. VNIPIpromtechnologii offers comprehensive engineering solutions ranging from conceptual design to equipment supply and installation.
The first comprehensive solution offered was a yellowcake dehydration method developed for Dalur, a Russian uranium manufacturer owned by Rosatom. The end-to-end services provided by the institute covered R&D, engineering, equipment procurement, customs clearance and installation. The new uranium pulp dehydration line at Dalur was put into operation in September 2015.
Another activity area of the institute is the development of recovery technologies for uranium and other minerals. In 2018, VNIPIpromtechnologii designed a facility for sorption recovery of rhenium from sulfuric acid solutions at a copper smelting plant operated by Kazakhmys. In 2019, the institute signed an agreement to design a carbon-in-leach (CIL) facility and provide consulting services for Clean TeQ Sunrise (Australia). The CIL facility designed by the institute will produce nickel, cobalt and scandium and will be a key element of the company’s production process.
VNIPIpromtechnologii keeps developing its competencies in industrial engineering and stay focused on winning more orders from mining companies from all over the globe.