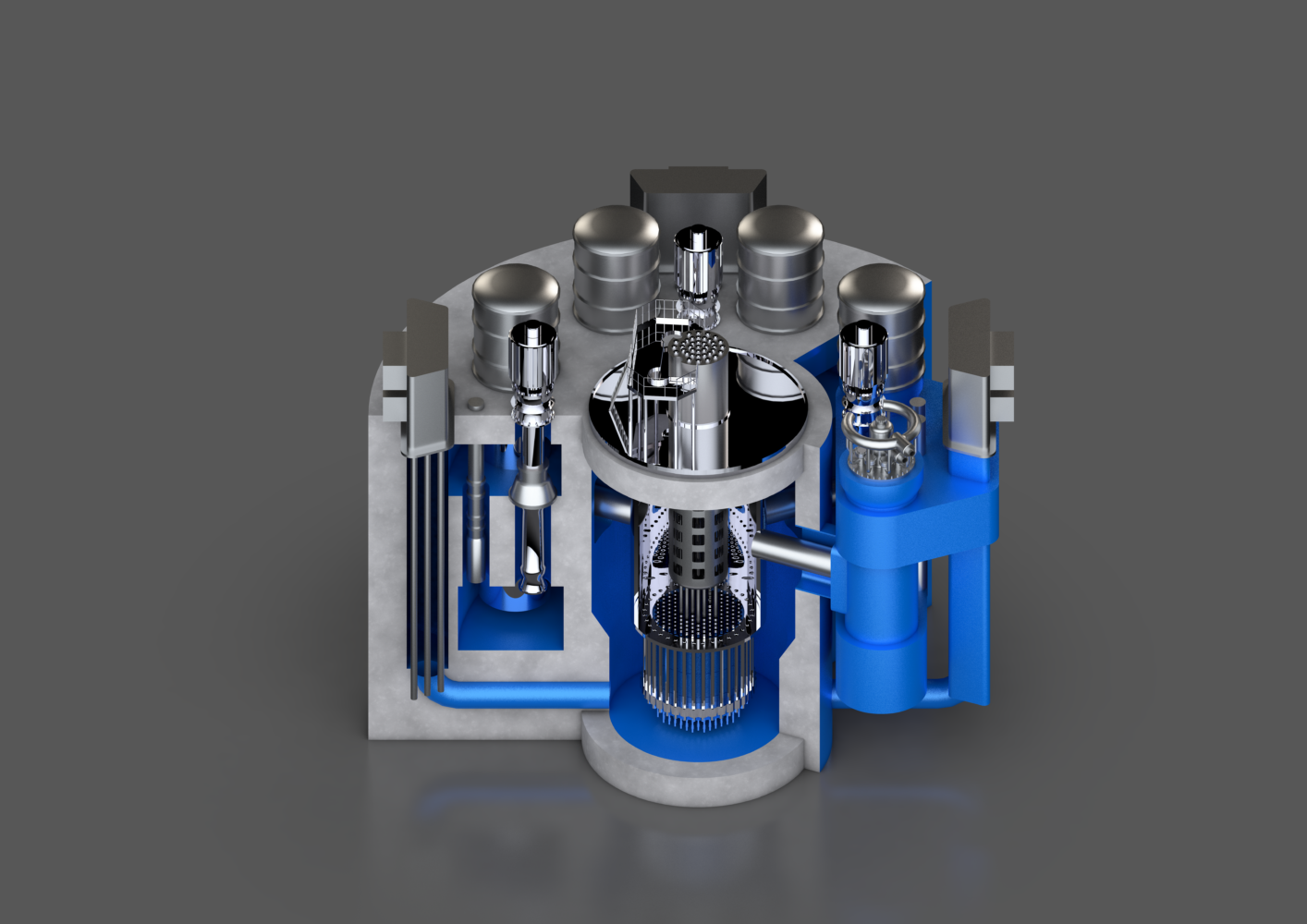
Lead-Cooled Reactor Made Tangible
back to contentsBREST-OD‑300 is the first lead-cooled nitride-fueled fast neutron reactor that brings theory into reality. Its key objective is to demonstrate the feasibility of the latest reactor technologies and the tangibility of closing the nuclear fuel cycle.
Reactor design and operation principles
BREST-OD‑300 is a Russian acronym for a “300 MW passively safe pilot demonstration fast neutron reactor.” It uses molten lead as a coolant and a mixture of uranium and plutonium nitrides (MUPN) as a fuel. The first concrete for the reactor’s basemat was poured in June 2021.
The new type of coolant necessitates a specific design: the core of BREST-OD‑300 is located in the central section of a reinforced concrete pool filled with molten lead. Its peripheral sections house steam generators and circulation pumps.
The melting and boiling temperatures and other physical properties of the coolant and the reactor design make it possible to omit the core catcher and many of the auxiliary systems and reduce safety requirements for the out-of-pile equipment. The integral design and physics of the BREST reactor exclude the possibility of accidents that would require evacuation of people.
The reactor has a two-circuit design: nuclear fuel heats molten lead in the primary circuit; molten lead then flows through a steam generator and transfers heat to water in the secondary circuit; water turns into steam and rotates a turbine generator to produce electricity.
BREST-OD‑300 is part of the so-called ‘pilot demonstration power production facility’ (abbreviated ODEK in Russian) that also includes a uranium-plutonium fuel fabrication unit and a spent fuel reprocessing unit. New fresh fuel will be produced there from reactor-grade plutonium and depleted uranium by carbothermal synthesis.
The three ODEK units are meant to demonstrate the sustainability of spent fuel recycling into fresh fuel, that is, the feasibility of a ‘closed’ on-site nuclear fuel cycle.
Multi-dimensional engineering
In late April, the Siberian Chemical Plant (SCP, part of Rosatom’s TVEL Fuel Company), ODEK’s host site, began to assemble a prototype pump for molten lead. Weighing over 30 tons, the pump is made of high-alloy steel grades and ceramic materials. Its parts were delivered to the site in late March 2023. When assembled, it will be tested on a dedicated test bench, in a column filled with molten lead. The pump is capable of pumping 11 tons of molten lead per second through the reactor’s primary circuit, which is comparable to the load of a medium-sized truck.
In 2023, the pump will be tested for pressure and flow performance. Based on the results obtained, the prototype design may be modified to manufacture four pumps for the reactor.
The Novosibirsk Chemical Concentrates Plant (part of Rosatom) is developing dummy fuel assemblies for the mock-up reactor core. They are planned to be ready at the end of 2024 and will be shipped to ODEK.
Fuel rods and fuel assemblies for BREST-OD‑300 have been thoroughly studied and tested boforehand. As a recent example, dummy fuel rods were tested in the IGR pulsed reactor (Kazakhstan). Completed in September 2022, the tests and subsequent post-irradiation studies confirmed the estimated performance of fuel rods in beyond-design-basis conditions, such as positive reactivity addition.
Meanwhile, researchers study new materials that could improve fuel performance. This February, VNIINM (part of Rosatom) produced a pilot batch of bimetallic tubes with a 0.3 mm thick ferritic steel protective layer. Such tubes can be used as fuel rod cladding in lead-cooled reactors and as a base material for the spacer grid cells in the reactor core. New structural materials will potentially increase the MUPN fuel burn-up in the lead-cooled fast reactors by 20–25 % and, consequently, make the reactor operation more cost-efficient.
Much work is also underway to improve employee qualifications. In March, over 30 employees of the ODEK fabrication/re-fabrication unit finished an analytical simulation course. They practiced operational skills, studied production processes and learned emergency procedures.
Later this year, SCP employees will do a two-week internship at the Beloyarsk NPP.
Reactor construction, equipment installation, development of the SNF reprocessing module and other works are fully on schedule. ODEK is planned to be commissioned in its entirety in 2030.