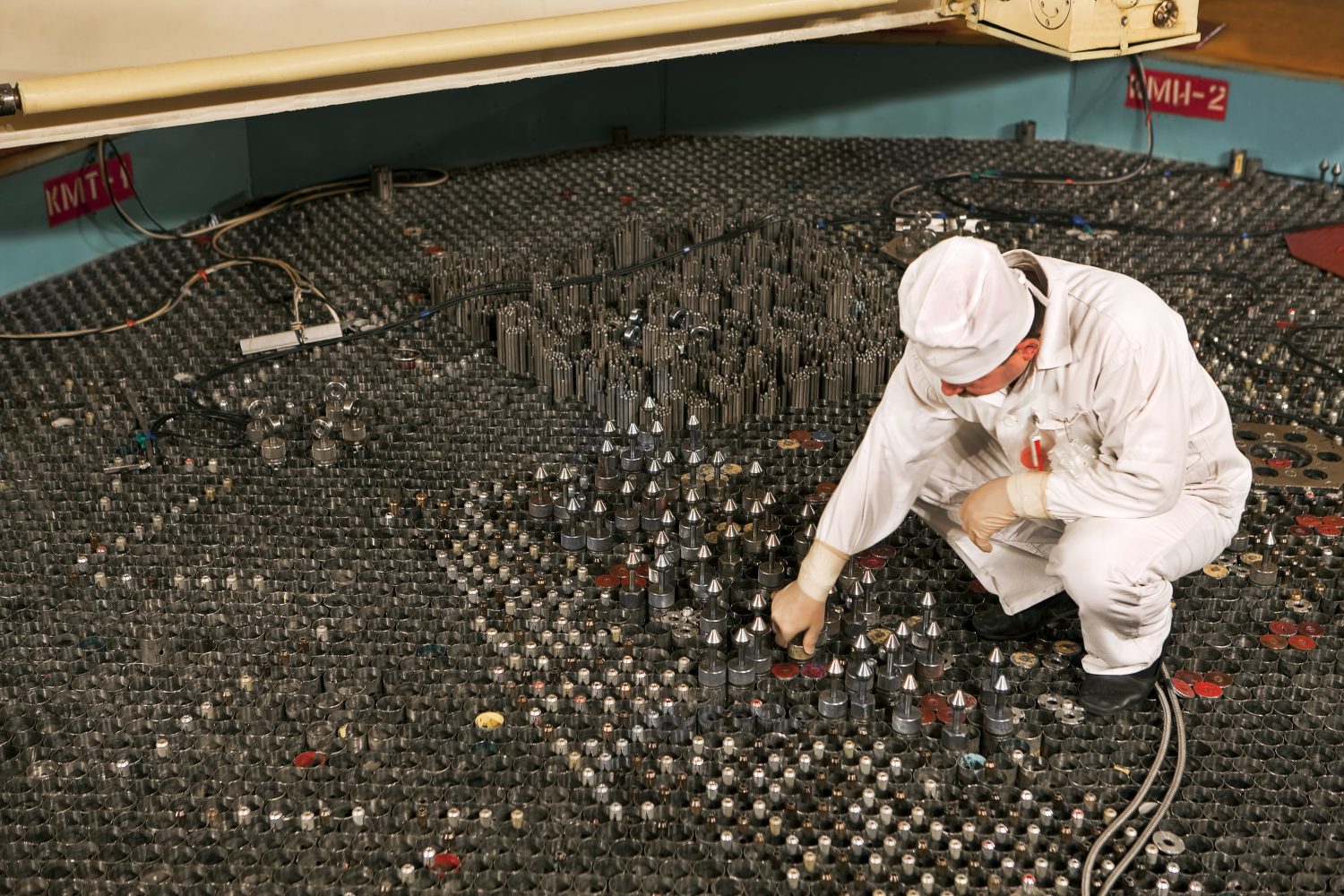
The Art of Combining Fuels
back to contentsAccident tolerant fuel
Accident tolerant fuel has been a priority area for the nuclear power industry over the past decade. The necessity to create nuclear fuel that would, to the maximum extent possible, help to avoid major accidents was recognized following the investigation into the Fukushima Daiichi accident caused by the shutdown of the cooling system and a steam-zirconium reaction at over 1,200 °C. At the moment, there are two ways to improve the technology, either by reducing the amount of zirconium in a reactor core or by increasing thermal conductivity of fuel by changing its chemical composition.
One should not think that the new fuel alone will prevent accidents. However, it might allow more time for response to rare incidents and accidents, while making the routine reactor operation more cost-efficient and more advantageous in terms of technology.
The engineering efforts are focused on creating both new cladding materials and fuel compositions. Chromium-coated claddings are believed to be the easiest of all possible solutions. Another interesting option, albeit requiring more detailed examination, is the use of silicon carbide composites as fuel claddings. For fuel compositions, researchers consider adding chromium or molybdenum and replacing uranium oxide with uranium silicide or uranium nitride.
Chromium coatings ensure higher corrosion resistance, durability and water permeability, thus, allowing zirconium alloys to remain ductile.
So far, there is no universally preferred coating technique, and many manufacturers are using solutions they find most suitable. For example, Alexei Yakushkin from the Pulsed Processes Department of the Troitsk Institute for Innovation and Fusion Research and Prof. Fyodor Vysikaylo from the Theoretical Physics Department of the Moscow Region State University, write in their article that thin film deposition methods, as well as heavy doping, are effective in terms of technology but very costly. Laser deposition techniques hold more promise, the authors believe. They also note that magnetron sputtering could be useful in coating fuel elements due to high deposition speed and homogeneity of coatings.
The new fuel compositions include doped uranium dioxide (UO2), high-density fuels (e. g. U3Si2) and metallic fuels (e. g. uranium-molybdenum fuel).
Keeping pace with the current trends, Rosatom is developing various combinations of claddings and fuel compositions. Last year, two pilot fuel assemblies were loaded into the MIR research reactor at the Research Institute of Atomic Reactors, with chromium-coated zirconium alloy and chromium-nickel alloy used as cladding materials. Their fuel compositions were based on the conventional uranium dioxide and uranium-molybdenum alloy with an increased density and thermal conductivity. Each fuel assembly consisted of 24 fuel elements with different combinations of materials.
That same year, Rosatom’s Bochvar Russian Research Institute of Inorganic Materials created samples of silicon carbide fiber with 10–12 % oxygen content. The next step would be to develop a technology to produce zero-oxygen carbide fiber that could be used in nuclear fuel cladding. The bank of samples is already in place, with brazing and sealing technologies being tested. The project will continue in 2021.
The pace of introducing accident tolerant fuel to the market will depend not only on the progress in research and development, but also on the feasibility of using specific accident tolerant fuels in specific nuclear reactors. Experience shows that this may take a few years.
Closed nuclear fuel cycle (CNFC)
In general terms, the CNFC concept suggests that spent nuclear fuel can be reprocessed and again loaded into the reactor. Some fuel compositions allow using up to 99 % of depleted uranium, which lies idle at storage facilities. This helps solving the problem of fresh feedstock for the nuclear industry and cutting down on waste. Another option is to burn highly radioactive elements called minor actinides.
Closed nuclear fuel cycle
Rosatom works systematically to create new types of fuel for the so-called closed nuclear fuel cycle.
The new range of fuels consists of three products — REMIX, MOX and MUPN, each being currently studied and tested.
According to the Rosenergoatom (Russian NPP operator, part of Rosatom), 26 MOX fuel assemblies are now used in the BN‑800 reactor. Eighteen of them contain pelletized MOX fuel and are the first standard fuel assemblies manufactured at Rosatom’s Mining and Chemical Plant and supplied to Rosenergoatom by Rosatom fuel company. They were loaded into the BN‑800 reactor at Beloyarsk NPP in late 2019. Another eight fuel assemblies, which contain vibro-packed MOX fuel, have been made at the pilot production line of the Research Institute of Atomic Reactors. The assemblies with pelletized MOX fuel will be irradiated for a year and a half, with the reactor to be refueled thrice during that period. By the time of unloading, these fuel assemblies will have worked for about 465 effective days. “At the moment, these fuel assemblies are functioning as designed, and have worked for about 310 effective days,” Rosenergoatom says.
The performance of pelletized MOX fuel has been confirmed by irradiating tens of pilot fuel assemblies in the BN‑600 reactor. Almost a quarter of the fuel initially loaded into the BN‑800 reactor, which was started up in 2015, consisted of MOX fuel assemblies manufactured at the pilot production lines of the Research Institute of Atomic Reactors and Mayak Production Association. The irradiation of these assemblies confirmed the reliability of pelletized MOX fuel. This allowed BN‑800 to run solely on pelletized MOX fuel, which was manufactured at the Mining and Chemical Plant (MCP).
Rosatom has already produced and supplied the first batch of 168 MOX fuel assemblies for refueling the entire reactor core at Beloyarsk NPP. These fuel assemblies will be loaded into the reactor in the first half of 2021. The transition to MOX fuel is expected to be completed in the second half of 2022. There may be minor shifts in the refueling schedule due to changes in the maintenance timeline.
Just like MOX fuel, REMIX fuel is a mixture of uranium and plutonium oxides but with lower plutonium content (1–3 wt%). Besides, REMIX fuel contains enriched uranium (ca. 3–4 wt% U‑235) instead of depleted one. Unlike MOX fuel, REMIX fuel is loaded into power reactors (VVER or RBMK), not fast breeders. One more difference is that REMIX fuel will be used with TVS‑2M fuel assemblies, which house more fuel than previous models and feature longer fuel rods (including those with uranium-gadolinium fuel) and racks, enhanced cell shape, and thinner bottom spacer grids.
Since 2016, three fuel assemblies, each containing six rods with REMIX fuel, have been piloted at Balakovo NPP Unit 3. Each fuel bundle has a total of 312 fuel rods. Their third 18-month irradiation cycle began in 2020. The next step will be the loading of fuel assemblies containing REMIX fuel only.
In August 2020, Rosatom’s Investment Committee decided to create a REMIX fuel bundling line at the Mining and Chemical Plant to provide the necessary number of fuel assemblies. The new line will be made by upgrading a pilot fuel fabrication line and adding the equipment for production of fuel elements and assemblies. It will be commissioned by 2021. Once the new production line is tested and the pilot fuel assemblies are unloaded at Balakovo NPP, Rosatom will decide whether to start commercial production of REMIX fuel.
What makes MUPN fuel different from REMIX and MOX fuels is that it is based on nitrides, not oxides (MUPN stands for Mixed Uranium-Plutonium Nitride). The fuel will be used in the BREST-OD‑300 reactor as part of the Breakthrough Project. It is also planned to load MUPN fuel into the BN‑1200 fast-neutron reactor, which is now at the design stage. The pilot fuel assemblies for the new reactor are now manufactured and tested in the BOR‑60 and MIR research reactors and the BN‑600 commercial reactor. More than 20 of them are being irradiated, with fuel burn-up already exceeding 9 %. Equipment installation is underway at the fuel fabrication/refabrication unit now built at the Siberian Chemical Plant for the BREST-OD‑300 reactor.
When organizing commercial production of REMIX, MOX and MUPN fuels, a crucial problem is proper management of high-level radioactive materials, particularly nuclear fuel that has been irradiated or reused for two or more times.
Enhancements also matter
Rosatom not only develops new fuel for new reactors, but also enhances the existing fuel types for its current customers. In October, the company completed a project set up in 2017 to introduce a modified version of fuel assemblies for VVER‑440 reactors at Hungary’s Paks NPP. Due to an optimized water-uranium ratio, the new fuel assemblies improve fuel utilization and make reactor operation more cost-efficient.
This July, Rosatom and the Czech energy company ČEZ a. s. signed an agreement to introduce RK‑3+, a new version of nuclear fuel for VVER‑440 reactors, at Dukovany NPP. The improvements on the previous version include replacement of ducts with gusseted framework structures, increased distance between fuel rods, and a modified cross-section enrichment profile. These improvements will extend the fuel cycles at Dukovany.
In accordance with the contract between Rosatom and Slovakia’s Slovenské elektrárne a. s., a project is underway to develop a new nuclear fuel and a new fuel cycle strategy for the Mochovce and Bohunice nuclear power plants. The new fuel will feature an optimized cross-section enrichment profile (with fuel elements placed depending on the U‑235 enrichment level) and fuel pellets made of a different uranium grade. The enhanced fuel is expected to extend the fuel cycle and improve the cost-efficiency of power units.
Plutonium in MOX fuel
The MOX fuel used in Russian fast-neutron reactors is a mixture of plutonium oxides with depleted or natural uranium. The mass fraction of plutonium reaches 15–25 wt% depending on enrichment region and plutonium isotope content. Pelletized MOX fuel assemblies may contain plutonium of various origins:
- Low-level plutonium (extracted by reprocessing spent nuclear fuel from sodium-cooled fast breeder reactors)
- High-level plutonium (extracted by reprocessing spent nuclear fuel from VVER reactors)
- Homogenized plutonium (a mixture of weapons- and fuel-grade plutonium; it is currently out of use as Russia has suspended the agreement on management and disposition of surplus weapons-grade plutonium, known as the Plutonium Management and Disposition Agreement).
The pelletized MOX fuel assemblies now irradiated in BN‑800 contain low-level plutonium. In 2021–2022, MOX fuel is planned to use high-level plutonium, which differs from low-level and homogenized plutonium in its isotope content. For instance, it contains more even-A isotopes accumulated during irradiation of nuclear fuel in power reactors (BN, VVER and RBMK).