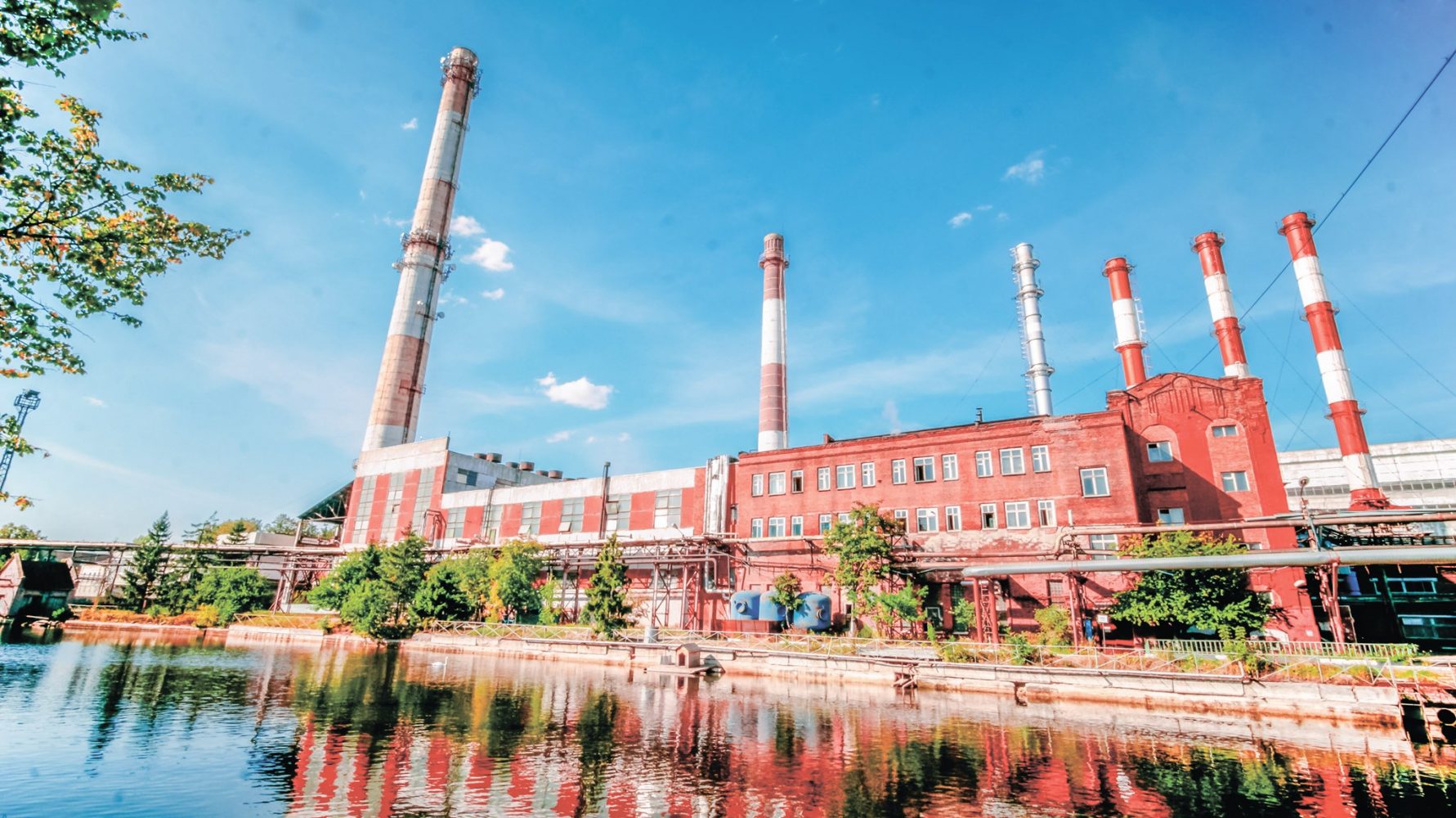
Sheikh’s Dream Rooppur
back to contentsAnatoly Smirnov, CEO of ZiO-Podolsk, met the guest and assured him that the production would be completed ahead of schedule and equipment would be delivered on time.
The Podolsk-based plant is manufacturing a separation tank of the steam superheater, a high-pressure preheater, and a passive component of the emergency core cooling system for Unit 2. ZiO-Podolsk has already delivered four separation tanks, four high-pressure preheaters, and a suppression pool for Units 1 and 2.
Kamrul Ahsan also visited RASU and met its CEO Andrey Butko. He said the coronavirus pandemic had not impacted the plant and its business. RASU is assembling and checking equipment for Rooppur Unit 1 and testing control systems. The work is expected to be completed in September 2020. As soon as technical audit is finished, all the systems and equipment will be sent to Bangladesh.
According to Kamrul Ahsan, the people of Bangladesh are looking forward to the start-up of the country’s first nuclear power plant in Rooppur, so it is important to synchronize the production of equipment at the plants and construction on the site. “The Rooppur NPP was a dream of the country’s founding father Sheikh Mujibur Rahman, and this dream is being fulfilled by his daughter, Sheikh Hasina Wazed,” Kamrul Ahsan said.
In their turn, the top executives of the Russian companies asked the ambassador to express their gratitude to the Bangladeshi Minister of Science and Technology Yeafesh Osman for his personal supervision of the construction project.
Other subsidiaries of Rosatom’s engineering division Atomenergomash are also involved in the production of equipment for Rooppur. Atommash, a Volgodonsk-based production facility of AEM Technologies (part of Atomenergomash) finished the welding of bottoms to the steam generator for Rooppur.
The process goes as follows. A red-hot workpiece is press-formed into the needed shape. Automatic welding is performed at a temperature ranging from 120 °C to 190 °C and usually takes 5 days. Making two welds required 700 kg of wire and 900 kg of flux. Then the welds are subjected to heat treatment and go through quality checks, including hydraulic tests and eddy current testing of the heat exchange tubes. The welding of the bottoms is the final stage of the steam generator assembly process.
Atommash also completed hydraulic testing of the first steam generator for Rooppur Unit 1. Hydraulic tests are an essential part of regular quality checks.
The tests run as follows: all the openings of the steam generator are first plugged up; the primary and secondary loops are filled with distilled water. Then water with a temperature of 350 °C is pumped into the primary loop at the pressure of 24.5 MPa (243 atm), while the secondary loop is filled with 300 °C water at the pressure of 11.45 MPa (115 atm). The testing pressure in the two loops is 1.4 times the working pressure.
Finally, Atommash completed fit-up tests on the reactor pressure vessel and reactor internals. The tests were conducted in an underground caisson. First, the 335-tonne vessel was sunk into the caisson, followed by the installation of key internals, such as an 11-meter 73-tonne core barrel, a 38-tonne core baffle and a 68-tonne protective tube unit. The workers installed fastening keys and fixed the components to align the reactor’s head.
At the moment, the Rooppur NPP is 30 % complete, with 27 % of estimated investments made. The coronavirus pandemic has not affected the construction process. The number of foreign employees was increased to meet the time schedule. “The on-site work gained momentum during the COVID 19 pandemic. At present, we are constructing the reactor building. The work is on a firm schedule,” Shawkat Akbar, Director of the Rooppur Project, told BanglaNews24.
The construction at Rooppur started in December 2017. The commissioning of Unit 1 is scheduled for mid 2023, with Unit 2 to come online in 2024. About 8,000 employees are involved in the construction project, including 1,800 workers from Russia. Nearly 2,000 foreigners are working on the construction site at present.
Sanitary regulations are strictly followed. Body temperature of every employee is taken at the entrance to the construction site. Employees with a fever are not allowed to enter the site and are quarantined for a week. They may return to work only after medical examination. In order to maintain social distancing, employees enter the site in small groups at different times. Social distancing is also maintained in the canteen. Separate housing is arranged for as well. Newly arrived foreigners and new employees should provide medical certificates confirming that they are COVID 19 negative. If a worker contracts the virus, all the employees working in the same shift are put into quarantine.
“Our goal for 2020 is to complete the reactor building for Unit 1, install the equipment in it and continue the construction of Unit 2. We will receive all the machinery and equipment for Unit 1 in the current year. Next year, we plan to complete the construction of the reactor building for Unit 2 and installation of the equipment,” Shawkat Akbar said.
Glossary
The nuclear reactor is a cylinder-shaped elliptical-bottom vessel that houses the core and internals. It has a hermetically sealed head with machinery drives installed on it.
The steam generator is a heat exchanging device that belongs to the nuclear island and is a safety class 1 product. It measures 14 meters in length and more than 4 meters in diameter and weighs 350 tonnes. Each reactor unit has four steam generators.