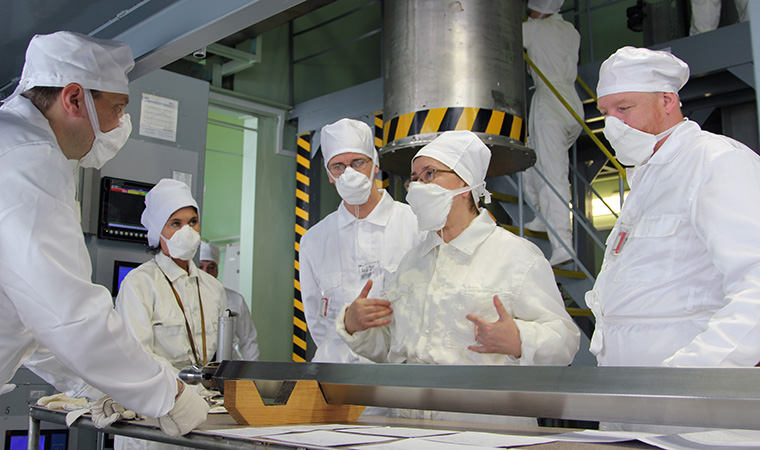
Fueling success
back to contentsRosatom has long been developing two new fuels for fast reactors – mixed oxide (MOX) fuel and mixed uranium plutonium nitride (MUPN) fuel – as part of its Breakthrough Project to close the nuclear fuel cycle and create an innovative nuclear fuel technology. The MOX fuel has long been used in sodium-cooled breeders, particularly in the operating BN-600 reactor. It will also be loaded in the BN-800 reactor, which is soon to generate power at the Beloyarsk NPP. It is not unlikely that the first commercial sodium-cooled reactor BN-1200 will also run on MOX fuel produced at the Mining and Chemical Plant in Krasnoyarsk Krai.
Along with MOX fuel, Rosatom is developing a totally different nitride fuel to be used as a primary fuel material in new BREST reactors (lead-cooled fast neutron breeder reactors). In-pile tests on fuel assemblies are now carried out at the Beloyarks NPP.
Experts are in no haste to make premature conclusions about performance of the new fuel until their have experimental evidence. Theoretical computations are impressive though. A MUPN fuel molecule is much more compact than an oxide fuel molecule and therefore allows for a higher concentration of nuclear fuel in the core. But its main advantage is a possibility of on-site reprocessing, without the need to transport it to other locations.
As compared to MOX fuel, MUPN fuel is more promising for the development of a closed fuel cycle. Its breeding ratio is 1.4 (instead of 1.2 for MOX fuel). It means that conversion of U-238 to Pu-239 in MUPN fuel is 20% higher.
In August, pilot nitride fuel assemblies ETVS-10 and ETVS-11 passed acceptance tests at SCP. According to Vyacheslav Glushenkov, Head of SCP Chemical Metallurgy Facility, SCP engineers have solid expertise in testing fuel assemblies – tests were completed ahead of the schedule.
Pilot nitride fuel assemblies are always made in pairs, for the BN-1200 reactor and BREST-OD-300 reactor. The fuel was designed and developed at A. Bochvar Russian Research Institute of Inorganic Materials (VNIINM). “The pair of ETVS-10 and ETVS-11 fuel assemblies has the same design as the previous pair, but has a specific in-pile test program,” said Mikhail Skupov, VNIINM Deputy CEO. Although the design is the same, fuel assembly ‘internals’ are different, stressed Dmitri Zozulya, Pilot Dense Fuel Project Manager. “We have changed the composition of fuel and claddings and used other steel grades,” he noted.
In general, the test procedure was routine and not as emotional as it used to be during the commissioning of previous assembly versions. But the expert panel was as demanding as before and strictly followed the procedure, starting with document examination and visual inspection and proceeding with weight and dimension measurements, etc. Experts asked designers questions and, when satisfied with answers, moved to the next stage.
The panel praised the quality of weld seams and professionalism of the welder. As Dmitri Zozulya explained, it is the only facility to use manual welding techniques – all other plants use automatic welding. The plant has trained highly-skilled professional welders whose work impressed the experts so much.
Experience gained in the manufacturing of ETVS-10 and ETVS-11 will be used in the commercial production. “Over 80% of pilot fuel assemblies manufactured at SCP are fit for operation. This percentage is typical of commercial production rather than piloting,” noted Mikhail Skupov. After the pilot tests are completed, fuel assemblies will be irradiated in the BN-600 reactor. “Post-irradiation studies of these assemblies will provide unique information which no one has ever obtained. It will be used to assess fuel performance for licensing purposes,” says VNIINM Deputy CEO.
Another pair of fuel assemblies to be tested next spring will have a larger fuel rod diameter. Mikhail Skupov explains, “ETVS-10 and ETVS-11 simulate performance of fuel assemblies in the core center while ETVS-12 through ETVS-15 mock up their performance in the periphery.”
“We have new goals ahead. We plan to construct a new test facility at SCP to simulate BN-800 conditions,” says Vladimir Troyanov, Chief Technologist of the Breakthrough Project. “It will bring us a huge step nearer to the closed fuel cycle. In 2016, we will launch the new test facility and begin the production in the subsequent year.”
At the same time, the Mining and Chemical Plant manufactured the first commercial MOX fuel assembly for BN reactors. It complies with all the requirements for the BN-800 reactor core at the Beloyarsk NPP. It proves feasibility of the project and closes an important pilot stage preceding the full-scale commercial production of MOX fuel, the Plant’s press release says. “Production of the first MOX fuel assembly means that we have finished a key task of the Federal Target Program. This is, in fact, the first achievement that testifies to the feasibility of the Program,” explains Vyacheslav Pershukov, Rosatom Deputy CEO and Breakthrough Project Manager.