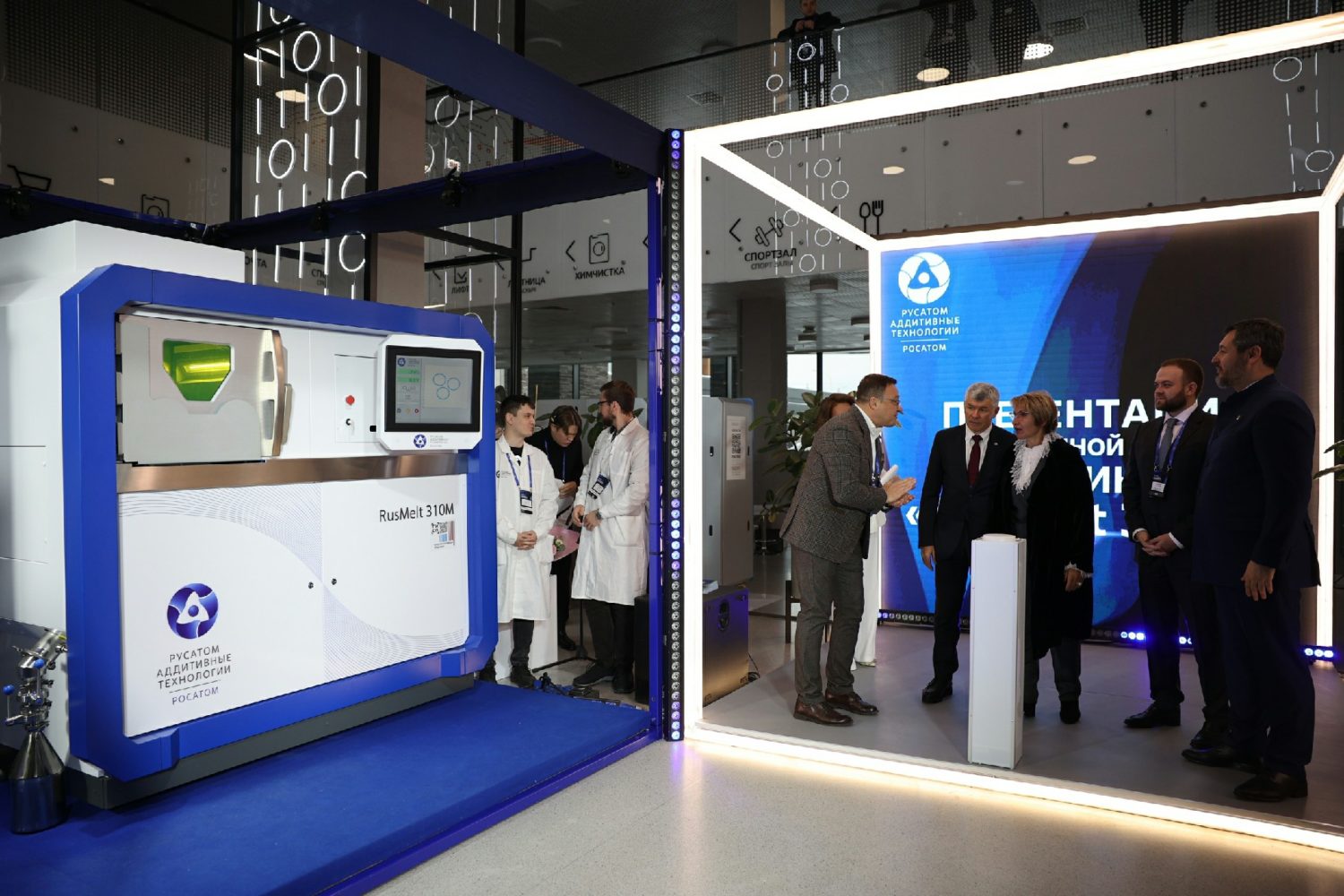
Реакторы печатные
вернуться к содержаниюВ этом году мы открываем новую рубрику – «Новые бизнесы», где будем рассказывать о тех направлениях деятельности Росатома, которые появились в структуре Госкорпорации сравнительно недавно и не относятся к основному бизнесу – созданию и эксплуатации атомных станций и ядерному топливному циклу. В этот раз речь пойдет об аддитивных технологиях.
О мировом рынке аддитивных технологий
Аддитивные технологии – это технологии создания изделий выращиванием из того или иного материала (металла, пластика, смеси песка и полимеров, бетона и т.д.).
В 2022 году в мире, по данным Wohlers Associates, лидерами в использовании аддитивных технологий были следующие отрасли: автомобилестроение (15,8%), товары народного потребления (14,5%), авиация и космос (13,9%). В 2021 году – авиация и космос (16,8%), медицина (15,6%), автомобилестроение (14,6%). Энергетика оба года занимала шестую строчку, но доля в 2022 году, по сравнению с 2021 годом, чуть подросла – с 7% до 7,8%.
Объем мирового рынка аддитивных технологий в 2022 году составил $18 млрд, из них $10,7 млрд пришлось на услуги, $3,8 млрд – на оборудование (3D-принтеры) и $3,3 млрд – на материалы.
Росатом в аддитивных технологиях
17 февраля Росатом заключил соглашение с правительством России по развитию аддитивных технологий в рамках Дорожной карты развития высокотехнологичной области «Технологии новых материалов и веществ».
Развивать 3D-печать Госкорпорация стала сразу в нескольких сферах. Во-первых, это производство металлических порошков и оборудования для такого производства. Во-вторых, создание 3D-принтеров, печатающих металлом. В-третьих, популяризация этой технологии как в российской атомной отрасли, так и за её пределами.
В 2014 году НПО «ЦНИИТМАШ» (входит в Росатом) выиграл грант Министерства образования и науки, а в 2016 году создал первый российский 3D-принтер. Он работает по технологии селективного лазерного сплавления (SLM). В 2019 году НПО «Центротех» (входит в Росатом) запустил в опытную эксплуатацию двухпорошковый двухлазерный 3D-принтер.
Также в «Центротехе» начали выпускать порошки для печати металлом. В ноябре 2020 года заработала установка «Капля» для выпуска порошков из «нержавейки», жаропрочных сталей, алюминиевых и медных сплавов. Она собрана из компонентов российского производства. Испытания химических и физических характеристик (гранулометрический состав, текучесть, плотность, форму частиц и проч.) подтвердили, что порошки полностью соответствуют требованиям и не уступают по качеству аналогам. С 2020 года на предприятии идет стабильный выпуск порядка 20 т порошка в год. Опыт «Центротеха» в Росатоме признали удачным, производство планируют расширять.
«Центротех» будет специализироваться на порошках из «нержавейки», а Чепецкий механический завод (входит в Росатом) – на порошках из жаропрочных сплавов и титана. Установка уже изготавливается, запуск ожидается в 2024 году.
Выпустив первые опытные принтеры, Росатом несколько лет совершенствовал их, в том числе – за счет использования комплектующих, созданных отраслевыми предприятиями или российскими партнерами. В мае компания-интегратор Росатома в области аддитивных технологий представила самый большой в России 3D-принтер, созданный в партнерстве с Санкт-Петербургским государственным морским техническим университетом. Он работает по технологии прямого лазерного выращивания (DMD) и может изготавливать изделия массой до 6 тонн. В частности – сложные по геометрии детали реакторных установок. Принтер DMD оснащен двумя промышленными роботами и позиционером.
В ноябре Росатом презентовал новую версию 3D-принтера RusMelt 310М, который выращивает изделия из металлических порошков по технологии селективного лазерного плавления (selective laser melting, SLM). Основные компоненты принтеров – лазеры и сканаторы, ПО и системы управления с различными датчиками – российского производства. Следующий шаг – создание принтера RusMelt 610 с рабочей камерой 600 мм по каждому из трех измерений.
Девять серийных принтеров готовы приобрести потенциальные заказчики. Мощности «Центротеха», который их выпускает, таким образом, загружены примерно на год вперед. Есть и новые заказы.
Росатом работает над тем, чтобы напечатанные изделия использовать для улучшения реакторных технологий. Многое уже сделано. Так, в следующем году пройдут испытания и подтверждение характеристик четырех изделий – рабочего колеса, клеммной коробки, вытеснителя и угольника. Первые два устанавливаются в насосах, вторые – в парогенераторном оборудовании. Следующий шаг – оформление технического решения на их использование в реакторной установке РИТМ-200. Предполагается, что уже в 2025 году их смогут устанавливать в реакторные установки для атомных станций малой мощности или новых атомных ледоколов. В Росатоме также намерены постепенно выйти на печать элементов реакторов малой мощности – над этим уже работает предприятие Росатома «Гидропресс».
Важное направление деятельности Росатома в области аддитивных технологий – популяризация этой сферы среди технологов и конструкторов машиностроительных компаний и потребителей их продукции. Для этого Росатом инициировал создание Ассоциации развития аддитивных технологий. В её задачи также входит консультирование заинтересованных сторон (госорганов, производителей, потребителей и т.д.), аккумулирование аналитики и подача предложений для формирования и улучшения нормативной базы.
Осваивая российский аддитивный рынок, Росатом также продвигает свою продукцию – принтеры и порошки – за рубеж, в дружественные страны. Переговоры с некоторыми из них уже идут.
Преимущества аддитивных технологий:
Сокращение сроков изготовления изделия из-за исключения дополнительных операций (создание заготовки, механическая обработка, соединение деталей).
Сокращение используемого материала до 80%.
Возможность упрощения изделия: вместо нескольких деталей или узлов можно вырастить одну целую деталь.
Улучшение характеристик изделия: меньше соединений – меньше вероятность поломок. Также можно снизить вес и использовать биметаллическую печать, чтобы получить сочетание свойств.
Сокращение сроков НИОКР благодаря возможности быстро проверить гипотезу.
Как следствие – более быстрый вывод изделия на рынок и в эксплуатацию.
Как следствие – более высокий доход.