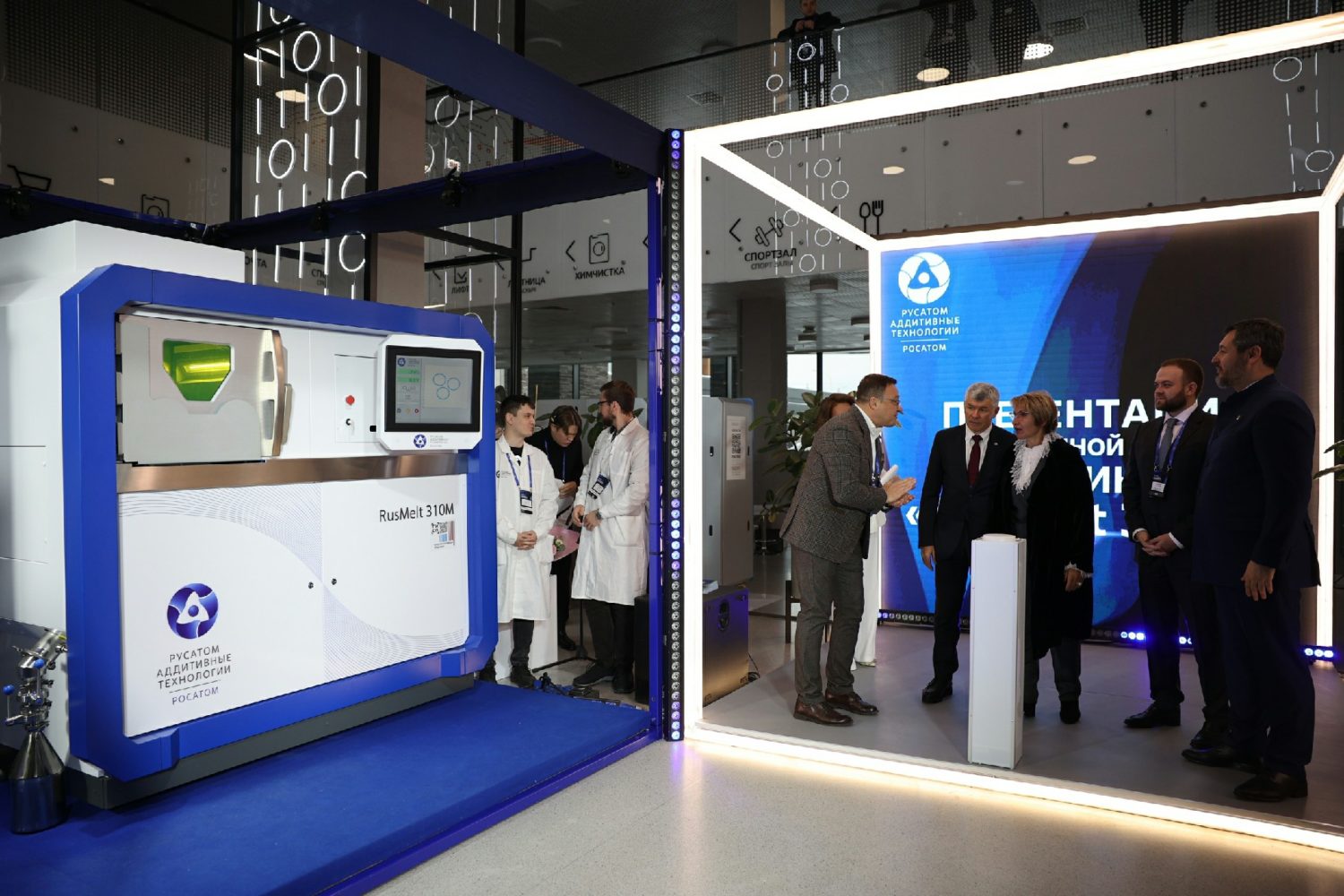
3D Printed Reactors
back to contentsThis article starts the New Businesses column dedicated to Rosatom’s relatively new business dimensions that extend beyond its conventional activities, such as nuclear construction and operation and the nuclear fuel cycle. This time we will tell you about additive manufacturing.
Global additive manufacturing market
Additive manufacturing is the process of creating objects by adding material (metal, plastic, sand and polymer mixtures, concrete, etc.) layer by layer.
In 2022, the sectors leading in the use of additive manufacturing were automotive engineering (15.8 %), consumer staples (14.5 %), and aerospace (13.9 %), according to Wohlers Associates. In 2021, they were aerospace (16.8 %), medicine (15.6 %), and automotive engineering (14.6 %). Power engineering ranked sixth in each of those years, but its share rose slightly from 7 % in 2021 to 7.8 % in 2022.
In 2022, the global additive manufacturing market totaled USD 18 billion, including services (USD 10.7 bn), 3D printers and equipment (USD 3.8 bn), and materials (USD 3.3 bn).
Rosatom and additive manufacturing
On February 17, Rosatom and the Russian Government signed an agreement to develop the additive manufacturing segment as part of the Technologies of New Materials and Substances roadmap.
Pursuant to the agreement, the Russian nuclear corporation will concentrate its efforts on several aspects of the 3D printing technology. First, Rosatom will be engaged in the production of metal powders and equipment for such production. Another area will be the development of metal 3D printers. Third, the company will promote the application of this technology in the nuclear industry in both Russia and other countries.
In 2014, CNIITMASH (part of Rosatom) won a grant from the Ministry of Education and Science and presented the first Russian 3D printer in 2016. It uses the selective laser melting (SLM) technology.
In 2019, Centrotech (also part of Rosatom) test-piloted a dual-laser dual-material 3D printer. Later, the company began to manufacture metal powders for 3D printing. Its Kaplya (Russian for ‘drop’) pilot unit for the production of stainless steel, heat-resistant steel, aluminum and copper alloy powders was put in operation in November 2020. The unit is assembled from Russian-made components. Chemical and physical tests on the particle size distribution, flowability, density, particle shape and other parameters of the powders confirmed that they fully meet all the applicable requirements and are not inferior in quality to alternatives. Since 2020, the company has been producing around 20 tonnes of powder per year. The pilot project was found successful, and Rosatom is planning to expand production.
Centrotech will specialize in stainless steel powders, while Chepetsk Mechanical Plant (part of Rosatom) will focus on heat-resistant alloy and titanium powders. A commercial production unit is already being manufactured and expected to be commissioned in 2024.
Having produced the first pilot printers, Rosatom spent several years upgrading them, including with the components manufactured by Rosatom’s subsidiaries and partner companies. In May, Rosatom’s subsidiary integrating additive manufacturing solutions and services presented Russia’s largest 3D printer developed in partnership with the Saint Petersburg State Marine Technical University. Using the direct metal deposition (DMD) technology, the printer can make products weighing up to 6 tonnes, particularly complex-shaped reactor parts. The DMD printer is equipped with two industrial robotic arms and a positioner.
In November, Rosatom presented an upgraded version of its RusMelt 310M 3D printer that makes items from metal powders with the SLM technology. Its key components, including lasers, scanners, sensors, control systems and software, are Russian-made. The next goal is to develop another RusMelt-branded printer with a 600x600x600 mm chamber.
Nine commercial printers have been ordered by customers, which means Centrotech will be working at full capacity for about a year to fulfill the orders. Meanwhile, new orders keep coming in.
Rosatom is working to improve its reactor technology with 3D-printed products. Much has already been done. For example, four printed parts — an impeller, a terminal box, a displacer and an elbow piece — will be tested next year to validate their performance. The first two pieces are parts of the pumps, while the other two are installed in the steam generators. The next step will be to justify and formalize their use in RITM 200 reactors. It is expected that as early as 2025 they will be installed in the reactors designed for small-scale nuclear power plants and nuclear icebreakers. Many components of small modular reactors might be 3D-printed in the future. Rosatom’s subsidiary Gidropress is already working on this task.
Rosatom is also investing much effort into raising awareness about additive manufacturing among the technical staff of mechanical engineering companies and consumers of their products. For this purpose, Rosatom initiated the foundation of the Additive Manufacturing Development Association. It provides, among other things, consulting services to different stakeholders (government agencies, manufacturers, consumers, etc.), accumulates analytical information, and prepares regulatory improvement proposals.
Developing the Russian additive market, Rosatom is also promoting its products — printers and powders — to international consumers in friendly countries. Negotiations with some of them are already underway.
Additive manufacturing advantages:
- Faster production time as no intermediate operations (such as blanking, machining, joining, etc.) are needed
- Up to 80 % less material used
- Less complex structure (a single piece instead of several parts or assemblies)
- Improved product performance (less chance of failure due to fewer joints). It is also possible to reduce weight and use bimetallic printing to get a combination of properties
- Reduced R&D time due to quick hypothesis testing
- As a consequence, shorter time to market and faster operationalization
- As a consequence, higher profit