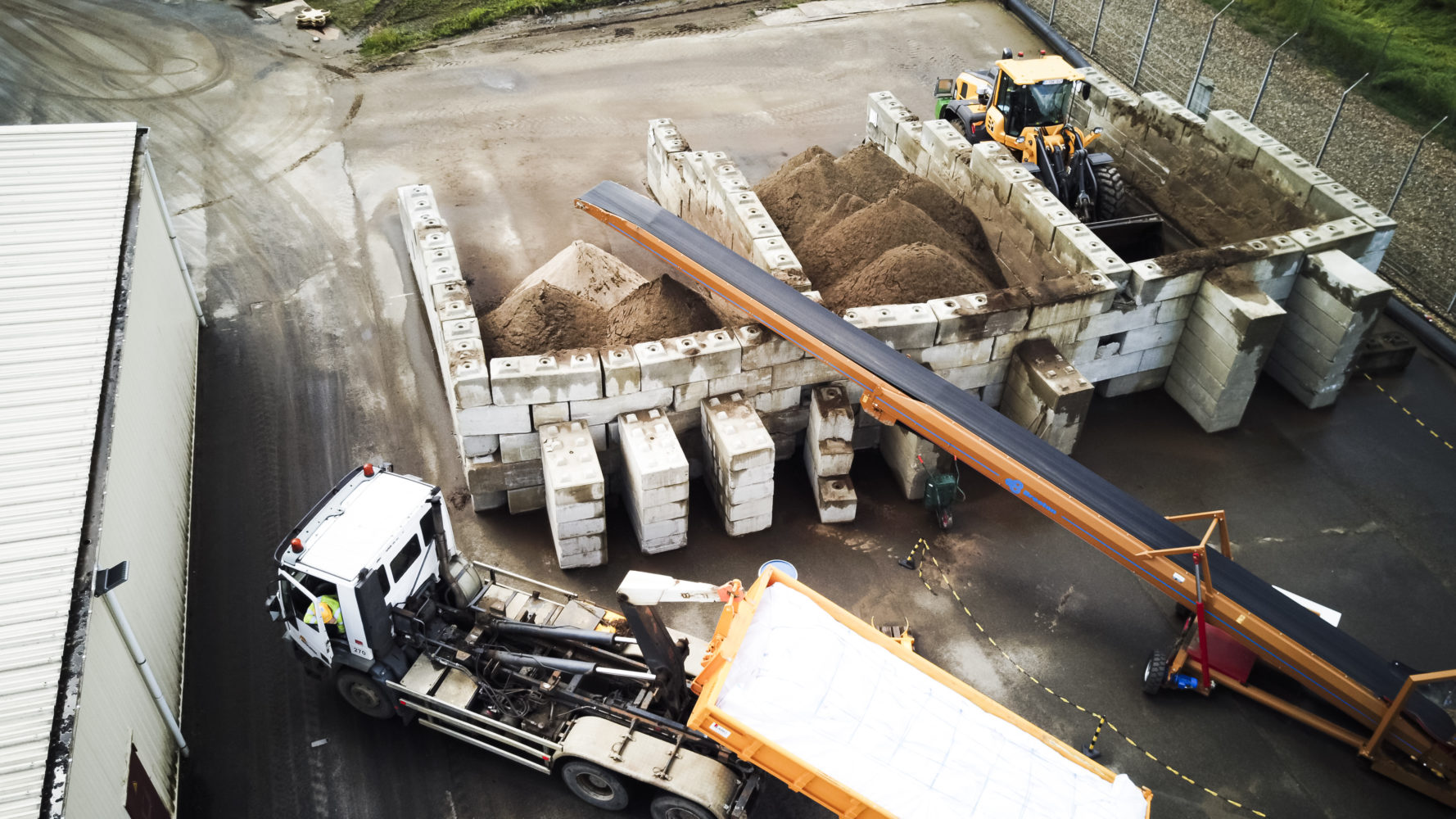
Nuclear Means Clean
back to contentsThe last month saw three major events for Rosatom in the back-end segment. First, Rosatom fuel division TVEL won a contract for bringing a mothballed uranium mine in Tajikistan to a safe state. Second, TVEL’s subsidiary Angarsk Electrolysis Chemical Plant received an automatic sorting line for radioactive loose materials. Third, TVEL took part in an IAEA seminar on decommissioning of small nuclear facilities.
TVEL Fuel Company is Rosatom’s subsidiary responsible for the development and fabrication of nuclear fuel. In 2019, the company became a nuclear industry integrator for decommissioning and radioactive waste management projects, technology and solutions.
Safe Taboshar
Taboshar, one of the early Soviet uranium mining sites, will be TVEL’s first nuclear legacy management project in the CIS countries. It will be carried out by the Central Design and Technology Institute (CPTI). As part of TVEL, CPTI functions as one of its competence centers for nuclear decommissioning.
The former mining site includes four tailings pads, Workshop 3 tailings storage facility, and a low-grade ore storage facility. In 1973–1975, all the pads were mothballed, and their surface and slopes were covered with soil. By contrast, heap-like tailings at Workshop 3 reach up to 70 meters and covering an area of 3 hectares while the low-grade ore storage facility has not been rehabilitated yet. Their surface and slopes are not protected against rain and wind, and radioactive materials are spread with airborne dust. There are dirt roads laid long ago and grazing lands all around, so the site requires rehabilitation.
By now, the company has conducted comprehensive engineering and topographic surveys, updated geological and hydrological parameters of the site, and prepared project documents and cost estimates.
“We will have to pull down the dilapidated low-grade ore plant, remove contaminated soil and replace it with clean one, reinforce the tailings storage slopes, cover up the surface of the tailings storage facility and install upper protection barriers, rehabilitate lower sections of the slopes, and install drainage and monitoring systems,” says CPTI General Director Mikhail Tarasov.
Contaminated areas were also found around the tailings storage facility. Radioactive soil will be moved to the tailings storage and covered up there. Clean soil for backfilling will be sourced from a number of mining sites in the region as specified in the project documents. The rehabilitation project is planned to be completed next year.
Separation of contaminated soils
The Angarsk Electrolysis Chemical Plant received FREMES (Free Release Measurement System) line for the separation of loose materials. It will be used in decommissioning operations at obsolete gaseous diffusion enrichment facilities (uranium is enriched using a gas centrifuge enrichment process).
It is assumed that the total amount of waste, which is estimated at 85,000 tons, will decrease 80 % thanks to waste separation. The separation line was first tested in a rehabilitation project at FBFC International’s fuel fabrication facility in Belgium. It processed over 45,000 tons of soils over 2.5 year, having reduced the amount of waste to be dumped significantly.
The line developed by TVEL engineers consists of three modules. The first module separates solid waste by sieving. Larger pieces are sent to crushing, while smaller pieces of up to 20 mm in diameter are fed to the second module. This is where the system analyzes their level of radioactivity and applies a predefined algorithm to divide the waste into three flows to be sent to the third module consisting of cascading belt conveyors and packaging machines. The first flow is a clean material; its radioactivity is less than one tenth of the regulated limit. The second flow contains a slightly contaminated material, from one tenth of the regulated safety limit and up to the safety threshold, that is treated before further use. Contaminated material in the third flow, which is radioactive above the regulated limit, is cleaned up or classified as radioactive waste and sent to storage.
The plant is capable of separating up to 10 tons of loose materials per hour. It is expected to be in use at the Angarsk Electrolysis Chemical Plant for the next five to eight years. “We expand our capabilities in nuclear legacy management and decommissioning thanks to FREMES technology and new competencies acquired by our staff,” project manager Igor Khisamutdinov says.
Attention to small nuclear facilities
TVEL took part in the Fifth Technical Meeting on the International Project on Decommissioning of Small Medical, Industrial and Research Facilities (MIRDEC). Led by the IAEA, the project was launched in the summer of 2018.
Although such facilities are usually low-power (up to 1 MW), the challenge is serious. If we take research reactors alone, there are more than 150 facilities worldwide either decommissioned or in the process of decommissioning; 20 reactors more are suspended or shut down and need decommissioning; another 45 reactors have been in operation for over 40 years. Apart from research reactors, there are a hard-to-estimate number of radiation sources, both secret and known to public, linear accelerators and other sources of ionizing radiation, and many of them require decommissioning.
The meeting featured reports on decommissioning of small nuclear facilities in the member states of the project, as well as expert discussions on the relevant topics, including sources of finance, relationships with regulating authorities, and disposal of decommissioned radiation sources used in medical applications.
Yulia Gorlova, Head of International Business Development at TVEL’s department for decommissioning programs, presented a report on the best Russian practices in decommissioning of research reactors, citing RFT and MR reactors at Kurchatov Institute as an example: RFT was the world’s first loop-type channel reactor for material studies, while MR was a multi-loop channel-type open pool reactor. Those reactors had somewhat more power and formally do not fit into the small facility category but their decommissioning is relevant in terms of challenges faced and therefore worth considering.
“Small nuclear facilities and reactors are often located in urban areas, while medical facilities are most often dismantled in the medical centers that continue their routine operations. This imposes more restrictions on the work to be done and makes it more difficult. It is not unusual that such facilities are installed in relatively small spaces, there is no standard equipment for decontamination, dismantling and disposal, and many more aspects need to be taken into account. All those factors make it necessary to prepare detailed decommissioning plans,” Yulia Gorlova pointed out.
Rosatom has a wealth of experience in back-end management. In 2008–2015, the company carried out 37 projects at seven sites as part of the first Nuclear and Radiation Safety national program. In total, 57 facilities were decommissioned, with another 13 prepared for decommissioning. At present, the company is involved in the projects provided for in the second Nuclear and Radiation Safety program covering 2016–2020 and a period until 2030.
Rosatom also targets international markets, offering its decommissioning and radioactive waste management services.