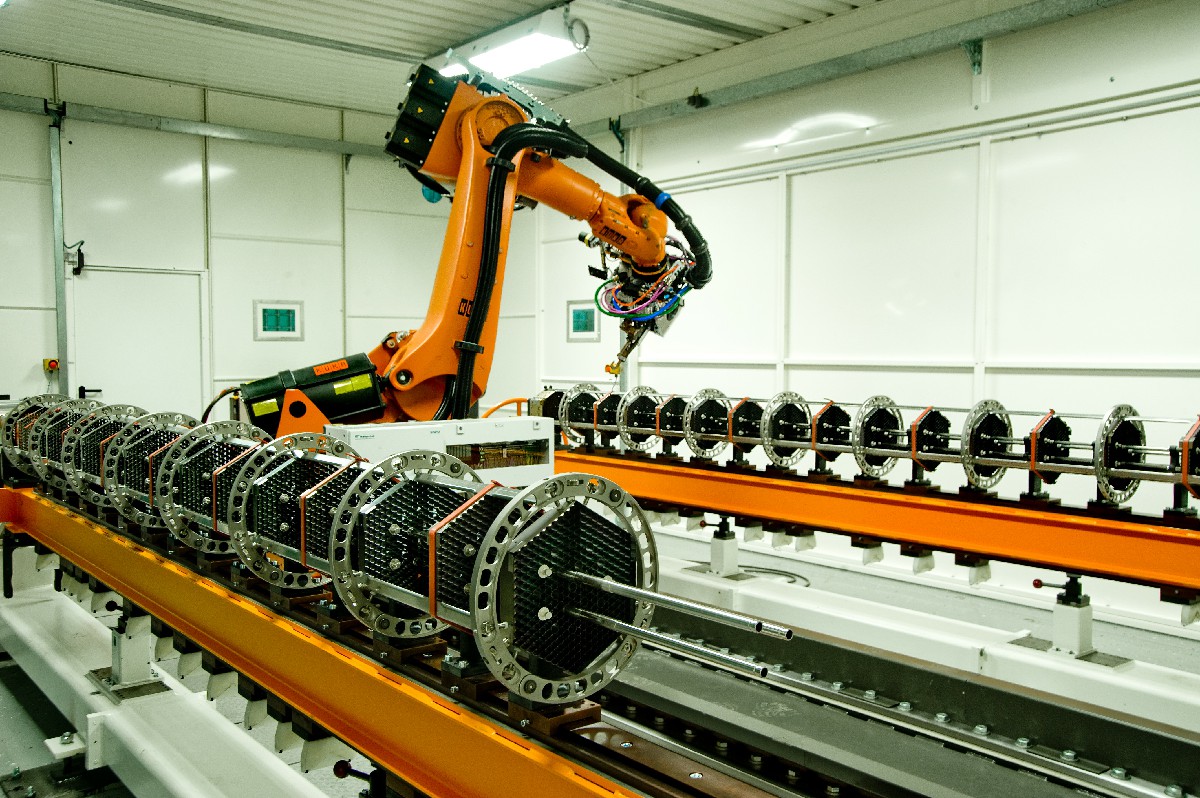
Nuclear Fuel: So New, So Different
back to contentsRosatom’s TVEL Fuel Company puts great effort into developing new types of nuclear fuel. They are needed to improve cost efficiency of the existing nuclear stations and run new reactors. Researchers and engineers recapped their work in 2022 at the New Generation of NPP Fuel: Developments, Operating Practices and Prospects conference.
Assembled by robots
The headline of the conference was, perhaps, an announcement that TVEL would manufacture the first three TVS‑5 fuel assemblies and load them into one of the reactors at the Novovoronezh NPP in 2023. What makes the new technology distinctive is a fully automated production that requires no human intervention. First, the technology will be tested to make sure that robots can manufacture fuel assemblies as well as humans do. If yes, a pilot production line will be launched in 2025 to manufacture TVS‑5 assemblies containing a uranium-plutonium mix (this is the fuel mix for which the new technology was developed). Until then, robots will assemble less sophisticated fuel rods made of ordinary zirconium claddings and a uranium oxide fuel composition.
The fully automated line for the production of TVS‑5 fuel assemblies will be built at the Siberian Chemical Plant in Seversk. The plant is gradually turning into a fuel hub for the closed nuclear fuel cycle as a fuel reprocessing unit and a fuel fabrication/re-fabrication unit for the BREST-OD‑300 fast neutron reactor are built on the same site as part of the Proryv (Breakthrough) Project.
“The Kurchatov Institute studied several options of the uranium-plutonium mix for TVS‑5, including three REMIX fuels differing in plutonium content, and one MOX fuel composition. In-pile tests on REMIX fuel began in 2021 as six pilot assemblies were loaded in the reactor of Balakovo Unit 1. This year [2022 — ed’s note] we are working to make MOX fuel assemblies for the MIR reactor. This is how we will ensure maximum flexibility and stand-by for optimizing nuclear fuel cycles in response to customers’ needs,” Senior Vice President for Research and Development at TVEL Alexander Ugryumov explains.
Closing the nuclear fuel cycle
Rosatom is heading for a closed nuclear fuel cycle, which needs a special fuel. Uranium extracted from irradiated fuel assemblies is processed into fuel that has been used at Kola NPP Unit 1 and some units of the Smolensk, Kursk and Leningrad nuclear power plants since the 2000s. TVEL has confirmed the possibility and expediency of using reprocessed uranium in VVER‑1000 reactors. “We are working with RosEnergoAtom [Russian NPP operator] to extend its application to VVER‑1000 and VVER‑1200 reactors,” Alexander Ugryumov said at the conference.
Konstantin Kurakin, Head of Fuel Cycles at the Kurchatov Institute, noted that fuel reprocessing could save up to 20 % of natural uranium depending on the cycle length.
New materials for accident tolerant fuel
TVEL conducts tests on a number of fuel compositions and cladding materials to create accident tolerant fuel. Researchers study 42CrNiMo (chromium, nickel and molybdenum) alloy, chromium coatings for zirconium claddings, and silicon carbide claddings. Alexander Ugryumov considers this material to be the most promising although it is hard to produce.
TVEL develops two fuel compositions, uranium-molybdenum and uranium silicide, for its accident tolerant fuel. They have high thermal conductivity, thus posing lower risk of fuel overheating and melting in loss-of-coolant accidents. Besides, they have a higher density and uranium content, which leads to a longer refueling interval. However, there are drawbacks, too. “The uranium-molybdenum technology has been validated, and relevant solutions tested in a research reactor. Costs of this technology are higher, though, than that of making conventional ceramic fuel. This is what we will work on,” Alexander Ugryumov pointed out.
The next step in the study of silicon carbide claddings is to verify the possibility of using uranium-molybdenum and uranium disilicide fuels with this cladding material.
Precise geometry
Work is ongoing to develop MUPN fuel (MUPN stands for mixed uranium-plutonium nitrides). According to Mikhail Skupov, Deputy Director of the Russian Research Institute of Inorganic Materials (VNIINM, part of Rosatom), detailed design of the fuel assembly for the first loading of BREST-OD‑300 was upgraded in 2021, and engineers are working to identify and mitigate burn-up decreasing factors. VNIINM has developed schematic designs of fuel rods for BN‑1200 and BR‑1200 reactors and made a number of fuel rod improvement proposals, such as making side recessions to decrease the volume of fuel pellets, fuel microalloying with aluminum nitride to increase shrinkage and decrease creep, and introducing a liquid-metal sublayer to increase burnup.
Minor actinides doomed
Curium, americium and neptunium are the most active elements in irradiated nuclear fuel. It is planned that these elements will be extracted, curium will be placed in storage while americium and neptunium will be loaded into a fast reactor and burnt up there.
The concept of burning americium and neptunium in the lateral blanket of a fast neutron reactor has been already developed, says Alexander Tuzov, Director of the Research Institute of Atomic Reactors (RIAR). Fuel rods containing americium and neptunium oxides (the so-called minor actinide burning rods, MABRs) are made through remote vibration compaction. Experimental MABRs were loaded into the BOR‑60 reactor core slots with different neutron spectra. The first post-irradiation analysis results have been obtained but irradiation continues. Engineers have also developed detailed designs of MABR assemblies.
Reliability of TVS-Kvadrat
One of the conference sessions was dedicated to nuclear fuel for foreign-designed light-water reactors. Its participants said that square fuel assemblies TVS-Kvadrat had passed qualification tests in the european-designed PWR‑900 reactor. After post-irradiation analysis results were published by an independent research center, TVS-Kvadrat fuel assemblies have enjoyed commercial success in the global market. This is the world’s only PWR nuclear fuel that is fully independent from the developers of the original reactor technology in terms of intellectual property rights and manufacturing processes and that has proved reliable and cost efficient.